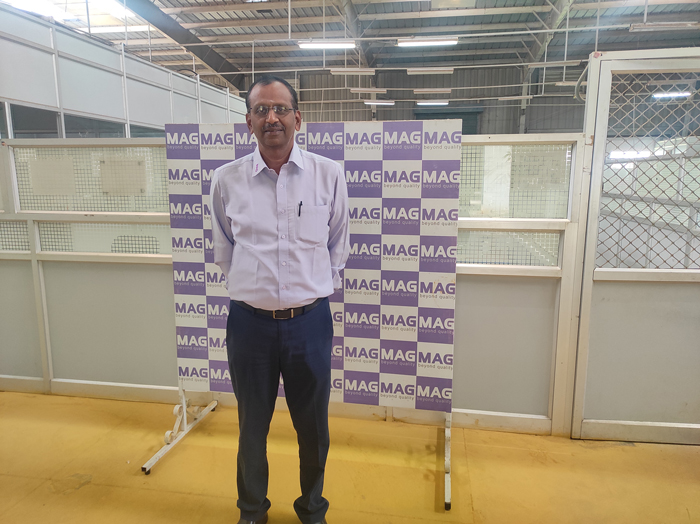
Automation is a major focus for MAG Solvics: C Dhandayuthapani
In this interview with Rakesh Rao, C Dhandayuthapani, MD, MAG Solvics, shares insights into innovations in testing technology, and how MAG is shaping the future of quality assurance in India’s evolving textile landscape.
As global demand for high-performance fabrics, technical textiles, and sustainable fibres accelerates, the need for reliable, accurate testing has become more critical than ever. MAG Solvics Pvt Ltd has been at the forefront of this transformation, empowering the textile value chain with cutting-edge testing instruments that ensure consistent quality from fibre to finished fabric. In this interview with Rakesh Rao, C Dhandayuthapani, Managing Director, MAG Solvics, shares insights into the company’s journey, innovations in testing technology, and how MAG is shaping the future of quality assurance in India’s evolving textile landscape.
How has MAG Solvics evolved over the years?
MAG Solvics Pvt Ltd was founded in 1991 by three young engineers with the vision to design and develop testing instruments specifically for the textile industry. Initially, we started with basic textile testing equipment, but over time, as the market evolved, we expanded our offerings to include advanced, high-value products. Since 2005, we have been manufacturing fully automatic testing systems such as cotton testing instruments and evenness testers. Today, MAG offers over 140 testing instruments that cover the entire textile value chain—from ginning to garments.
Our operations are fully integrated. We have our own R&D centre, recognised by the Government of India, as well as in-house manufacturing, assembly, and component fabrication units, spread across a 6,000 sq m campus. Since 2009, we have been operating from our current facility, which includes four dedicated blocks for fabrication, assembly, and commercial operations. Over the years, exports have grown significantly and currently account for 40–50% of our business. Quality and innovation remain the cornerstones of MAG’s success.
What are some key milestones in MAG’s growth journey?
A significant milestone was our transition in 2005 to high-value testing systems, which strengthened our position in the market. In 2015, we ventured into spindle monitoring systems, which contributed substantially to our growth. Today, over 3.5 million spindles are monitored using MAG’s systems, both in India and internationally.
Another major development came in 2016, when we established our in-house component manufacturing division. Previously, we outsourced these operations, but now, with our own CNC machines, nearly 80% of components are produced internally. For specialised components, we partner with approved vendors and supply our own raw materials, ensuring consistent quality. Importantly, there is no distinction in quality between our domestic and export offerings—our commitment to quality and service is uniform across markets.
How is MAG Solvics supporting the industry’s shift towards man-made fibres (MMF) and technical textiles?
We have proactively upgraded our existing testing instruments to cater to MMF and technical textiles. During the COVID-19 pandemic, we adapted our equipment to test materials such as face masks and gowns based on international standards. Additionally, with the rising demand for linen, we have modified our systems to test specific parameters of linen fibres.
Regenerated fibres are also gaining momentum, especially in regions like Panipat. These fibres often contain a mix of cotton, synthetic fibres, and yarn waste. To address this, we are enhancing our testing equipment to identify blend proportions, unwanted yarn bits, and immature fibres—critical factors in assessing the quality of regenerated fibres.
Is there a growing awareness around quality among manufacturers and end-users?
Absolutely. Quality is no longer an afterthought but a primary expectation across the value chain—from small-scale producers to large mills. Even in open-end spinning, where the emphasis on quality was once minimal, there is now a demand for precision testing. The trend is encouraging, and we are seeing increased enquiries from small manufacturers who recognise the need for reliable testing solutions. This shift is also driven by new regulations, such as the proposed QCO (Quality Control Order), which—although postponed—has already influenced purchasing behaviour in anticipation of mandatory testing norms.
How do you view Coimbatore’s role in the growth of India’s textile sector?
Coimbatore has always been a hub for the textile industry and continues to be a stronghold for spinning, machinery manufacturing, and innovation. While the pace of growth in the textile segment has moderated in recent years, there is increasing diversification into non-textile sectors such as motors, electronics, and components for defence applications. So, while textile growth may not be exponential, the region overall continues to thrive as an industrial base.
Specifically, in textiles, there is a notable shift from cotton-based spinning to synthetic fibre production. Areas like Erode are now primarily focused on viscose and other synthetic yarns. This change is driven by challenges in cotton sourcing—especially with Gujarat becoming the dominant cotton-producing region. Rising transportation costs have made synthetic fibres a more economical option for mills in the South.
Do you see MMF and technical textiles as the future of the industry?
Very much so. The shift is already underway. Several mills that previously focused exclusively on cotton have now diversified into MMF. This transformation is being supported by knowledge partnerships and government initiatives promoting technical textiles and synthetic alternatives.
Given the global trends and India’s push towards MMF and technical textile innovation, we see this as a critical area of growth for the industry and for MAG. Our team is actively modifying and developing instruments to meet these new requirements, and we are confident of playing a key role in enabling this transition.
What are MAG Solvics’ growth plans for the future?
Automation is a major focus for us moving forward. We have a detailed roadmap for the next five years, with plans to introduce more automation-led products that reduce manual intervention and improve operational efficiency. One such area is auto-piecing in spinning—where we aim to develop systems that automatically identify broken ends and initiate piecing without operator involvement. As the industry grapples with labour shortages, demand for such automation is rising.
Additionally, we are integrating IoT across our product portfolio to enable remote monitoring, predictive maintenance, and data-driven decision-making. All new equipment being developed will be IoT-enabled by default.