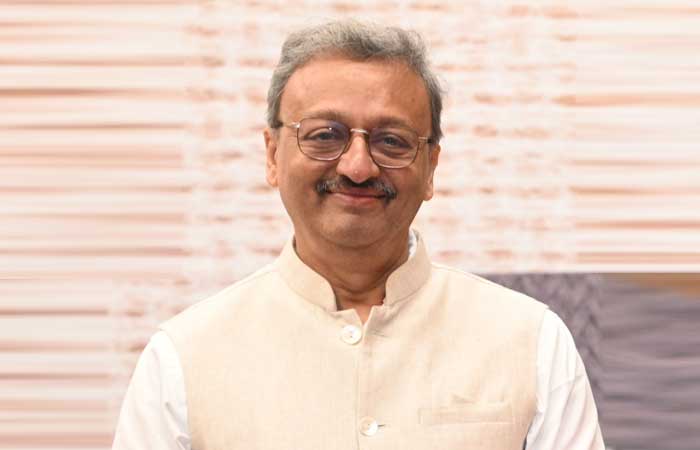
ATIRA is developing fully degradable or recyclable FRP composites: Pragnesh Shah
Ahmedabad Textile Industry’s Research Association (ATIRA) is an internationally renowned textile research institute for the textile allied industry. Established in 1947 by the textile mills of Ahmedabad as autonomous non-profit R&D institution the activities of the institution cover all aspects from fibre to finished fabrics in traditional textiles as well as technical textiles in the arena of geo-textiles, nano-web technology and composites. Pragnesh Shah, Director, ATIRA, in this interview with Divya Shetty, shares how his association is contributing to the entering technical textiles sector of India.
What is your assessment of the current state of the Indian technical textile industry, particularly in the areas of innovation and global competitiveness?
The Indian technical textile industry is expanding rapidly, especially in key sectors like defence, healthcare, aerospace, and infrastructure. However, innovation in the sector is still in its infancy compared to global leaders such as Germany and the US, where advanced materials and digital manufacturing techniques dominate. To close this gap, India must significantly increase its investment in R&D and embrace technologies like Industry 4.0, AI-driven textile production, and advanced material science. Initiatives such as promoting R&D, supporting startups, facilitating skill development etc. under the National Technical Textiles Mission by Ministry of Textiles, Government of India, are highly promising and play a pivotal role in shaping the future of the industry. These programs have been instrumental in driving innovation, boosting domestic capabilities, and positioning India as a key player in the global technical textile market. However, there is a pressing need for more cross-sectoral collaboration between industry, academia, and research institutions to foster sustained innovation and global competitiveness.
At present, both globally and in India, innovation is primarily focused on three key areas:
- Enhancing the functionalities of existing technical textiles
- Developing smart technical textile materials and products
- Closed-loop recycling of technical textile products for sustainable growth
How is the Ahmedabad Textile Research Association contributing to the advancement of the technical textile sector in India, particularly in the development of high-performance fibre-reinforced composites?
ATIRA, through its Center of Excellence (COE) in Composites, is driving innovation across design, development, and manufacturing, with a prime focus on building deep expertise and knowledge to ensure we remain at the forefront of critical sectors like aerospace, defence, and infrastructure. Currently, India contributes only 2 per cent of the world’s composites production, while the global composites market is projected to reach $93.7 billion by 2028. However, India’s composites market is expanding rapidly, with an estimated growth to $3.2 billion by 2028.
To capitalise on this growth, ATIRA is developing advanced solutions, such as smart fibre-reinforced polymer (FRP) composites, leveraging the properties of nanomaterials like graphene and carbon nanotubes. These smart composites are being designed for cutting-edge applications in aerospace, drones, defence, and construction, where traditional FRP materials have limitations. Additionally, we are advancing biocompatible FRP composites using natural fibres and biopolymers, and have developed highly flexible FRP composites with a newly engineered flexible epoxy resin, particularly suited for aerospace applications like deployable antennas.
Recognising the need for a strong prepreg industry, ATIRA is pioneering high-performance prepreg material development and has the capacity to produce glass fibber prepregs, positioning us to reduce import reliance and boost local manufacturing. Composites being a highly interdisciplinary field, ATIRA has established collaborations with key industries, national R&D organisations, and academic institutions. Notably, we have collaborated with Ahmedabad University to launch an M Tech program in Composites, fostering the next generation of talent in this critical field. Additionally, we are launching a Skill Development Program for the composite industry, supported by the National Technical Textiles Mission of the Ministry of Textiles, to enhance industry expertise.
Our comprehensive approach includes internships and training programs for industrial personnel and students, ensuring knowledge dissemination and skill-building for India’s growing composite market, aligning with the country’s goals for self-reliance and global competitiveness.
Your research focuses on enhancing the mechanical performance of fibre-reinforced composites using nanomaterials. How do you see these impacting industries like aerospace and defence in the near future?
ATIRA is developing FRP composites with significantly enhanced mechanical properties by harnessing the potential of nanomaterials such as graphene and carbon nanotubes. These nanomaterial-modified FRP composites, with improved mechanical properties, have the potential to improved product performances, durability, and reduce product weight by up to approximately 25 per cent, which is a substantial advantage in aerospace and defence sectors. Note that the weight reduction in FRP products can lead to lower operational costs, improved performance, and a significant reduction in CO2 emissions in these fields.
In terms of improving electrical conductivity in fibre-reinforced composites, what are the most promising applications you’re currently exploring, particularly in sectors like EMI shielding, sensors, and aerospace?
As you know, conventional FRP composites are non-conductive due to the non-conducting nature of the polymer matrix and fibres (except for carbon fibres). However, introducing electrical conductivity in FRP composites can open up new possibilities, especially in applications such as EMI shielding, reflector antennas, slotted waveguide antennas, strain sensors, de-icing, and protection from lightning. Currently, metal foils and coatings are used to achieve electrical conductivity in these composite products. Despite the good conductivity of metals, they have drawbacks such as higher density, and delamination of the metal from the FRP surface is common due to dissimilar surface chemistry, which affects the product’s longevity. Additionally, the maintenance costs of these metal-coated FRP products are very high. Therefore, ATIRA is working on replacing metal in these FRP composite products and has developed highly conductive, metal-free FRP composites. We are exploring their applications in aerospace, EMI shielding, and sensors.
Graphene-based e-textile sensors are revolutionising wearable technology. What potential do you see in healthcare, safety, and security sectors for these innovations?
Apart from smart FRP composites, ATIRA is also developing smart textiles, particularly electronic (e)-textiles, using graphene. The projected global market value for e-textiles and smart clothing is expected to reach approximately $15 billion by 2028. Graphene-modified textiles have immense potential in various fields due to their unique properties, such as being antibacterial, antimicrobial, lightweight, and providing sensing capabilities, thermal cooling and heating, abrasion resistance, and electrical and semiconducting properties. Wearable, highly sensitive, and selective physical and chemical sensors can be developed using graphene-based fabrics (third-generation e-textiles). These sensors can be used for diagnosing and monitoring human health, accurately predicting patients’ health conditions. Graphene-based textile electronics can also be employed for patient care and diagnosis in remote areas. Additionally, graphene-based textile strain sensors can be applied in safety and security sectors. At present, ATIRA is working on the large-scale production of graphene-coated fabrics and collaborating with industry to develop fatigue detection vests for industrial workers.
How does your association plan to contribute to sustainable growth through innovations like graphene/CNT-based natural fibres for more eco-friendly and stronger composites?
As you know, conventional manmade fibres are primarily derived from petrochemicals, which raise serious environmental concerns worldwide. While the recyclability of man-made fibres is a positive step toward sustainability, replacing conventional petrochemical-based fibres with more sustainable alternatives remains crucial to addressing the broader environmental concerns, especially when it comes to biodegradability. India produces a wide variety of natural fibres, including jute, cotton, bamboo, banana, and pineapple. However, these natural fibres suffer from poor mechanical properties and high-water absorption. Graphene and carbon nanotubes possess unique physical and chemical properties. ATIRA has developed graphene and carbon nanotube-modified natural fibres and resin. Through these modifications, ATIRA has created natural fibre-reinforced polymer composites with enhanced mechanical and physical properties compared to conventional composites made from unmodified natural fibre and polymer matrix. ATIRA is focusing on two main objectives in this area:
- Replacement of man-made fibre-based composites, particularly glass fibre-based composites, with nanomaterial-modified natural fibres where applicable.
- Development of fully recyclable or degradable high performance FRP composites for sustainable growth.
What are the key innovation strategies and areas of research that the Ahmedabad Textile Research Association plans to focus on in the next 5-10 years to stay ahead in the technical textile industry?
We have launched several R&D initiatives with the goal of reducing or completely eliminating the import of various technical textile materials and products. These initiatives are like laying the foundation for self-reliance in the technical textile sector. Here are the key plans we are currently pursuing:
- We have established a dedicated research group focused on enhancing the functionality of FRP composite products by harnessing the unique properties of nanomaterials. It’s like adding advanced features to a familiar product to make it smarter and more efficient.
- A specialised research group has been set up to focus entirely on the development of smart textiles, much like assembling a team of experts to build the ‘wearable technology’ of the future.
- We are working to improve the properties of Indian natural fibres and their related products.
- We are developing fully degradable or recyclable FRP composites with high mechanical strength. This is akin to creating eco-friendly products that are not only strong but also gentle on the environment, contributing to sustainability.