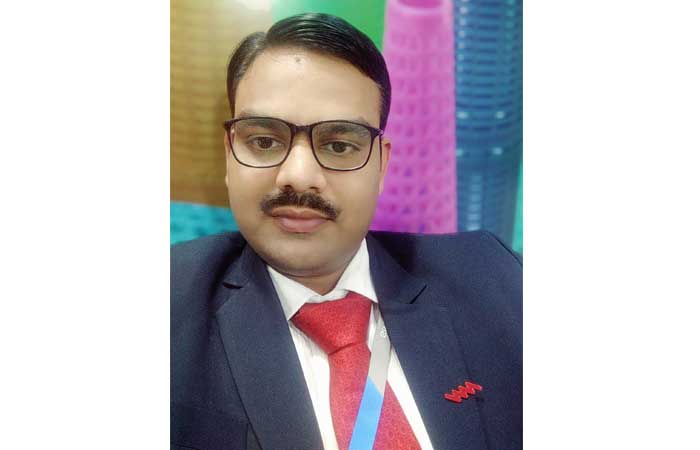
Anil Yadav: The industry is experiencing significant growth driven by domestic demand and export opportunities
Moksha Thermoplastics, based in Ahmedabad, Gujarat, is a largest manufacturer of Engineered yarn carriers for the textile spinning industry. The company offers a diverse range of products designed to enhance efficiency and quality in yarn Manufacturing & processing. Anil Yadav, Head – Technical Marketing & Development, Moksha Thermoplastics, explains the company’s current offering and future plans in this interview.
How is your company serving customers from the textile & apparels (T&As) segment?
Moksha Thermoplastics offers a diverse range of products designed to enhance efficiency in the textile industry. Our product lineup includes Speed Frame Bobbins and Roving Bobbins, along with Ring Spinning Tubes, which are compatible with both manual and auto-doffing ring frame machines across various makes. The Slim Line Series Ring Tubes stand out as innovative, lightweight solutions that reduce energy consumption, increase yarn capacity per tube, and improve overall spinning efficiency. Additionally, the company provides High-Temperature Yarn Carriers, capable of withstanding temperatures up to 140°C, making them ideal for yarn conditioning processes. Their range also includes Plastic Cones and Cheeses, available for both single-use and multiple in-house processing cycles, offering durability and cost-effectiveness.
Moksha Thermoplastics plays a crucial role in the textile spinning and yarn processing industry by addressing key operational needs. The company enhances efficiency by providing high-quality yarn carriers, such as slim tubes, which ensure smoother operations, minimise downtime, and boost productivity. Its products are designed to improve yarn quality, maintaining consistency and resulting in superior end products. Moksha also supports the industry’s transition towards automation with offerings like auto-doffing tubes, reducing reliance on manual labour and minimising errors. Additionally, the company is committed to innovation, continuously developing new solutions, such as slim line tubes and high-temperature yarn carriers, to meet the evolving demands of the industry.
According to you, what is the present state of the Indian T&As industry and textile machinery & accessories (TMA) industry?
As of February 2025, the Indian textile industry is experiencing significant growth and transformation, driven by both domestic demand and export opportunities. The sector is projected to expand from its current valuation of $138 billion to $195 billion by 2025.
Despite the positive outlook, the industry faces challenges such as fluctuating cotton prices, diminishing demand, capacity under-utilisation, and competition from imported fabrics and garments. The total imports of knitted fabric in FY 2022-23 were Rs 60.73 billion, with imports from China and Bangladesh posing significant competition.
The Indian textile sector has set an ambitious target of achieving $350 billion in market size by 2030. In your opinion, what are the significant challenges or barriers that could hinder this progress?
The Indian textile sector’s target of reaching $350 billion by 2030 is ambitious, and while the sector has significant growth potential, there are several challenges and barriers that could hinder this progress:
Fluctuating raw material prices: The price volatility of key raw materials, especially cotton, can affect the profitability of textile producers. Global supply disruptions, such as those caused by weather events or geopolitical tensions, can lead to inconsistent pricing and challenges in maintaining stable production costs.
Global competition: India faces stiff competition from other low-cost textile manufacturers like China, Bangladesh, and Vietnam. These countries often benefit from lower labour costs, more established infrastructure, or favourable trade agreements. As global markets become more competitive, India will need to find ways to differentiate its offerings, especially in high-value-added products such as technical textiles.
Sustainability pressures: As sustainability becomes a key focus for global consumers and governments, the textile industry will face pressure to adopt eco-friendly practices. While some progress is being made, the shift towards sustainable production methods—such as reducing water usage, waste, and carbon emissions—requires significant investment. Brands will need to balance environmental concerns with profitability, which can be challenging, particularly for small and medium-sized enterprises.
Labour shortages and skill gaps: The textile industry is labour-intensive, but India faces skill gaps in both high-tech manufacturing and quality control. There is a need for upskilling workers to handle modern machinery and to meet global quality standards. Moreover, as the industry becomes more automated, there will be a need for specialised technical expertise, which is often lacking in the workforce.
Infrastructure limitations: Although India has made strides in improving infrastructure; challenges remain, especially in logistics and transport. Efficient infrastructure is crucial for meeting export demands and facilitating the smooth movement of goods across the country.
Regulatory and policy issues: The textile industry is subject to a range of government policies and regulations, which can be complex and subject to frequent changes. While the government’s push through initiatives like the Production Linked Incentive (PLI) scheme is encouraging.
Over-dependence on traditional textiles: While India excels in the production of cotton-based textiles and traditional handloom products, it still faces challenges in diversifying its output to meet global demand for high-performance textiles, such as those used in automotive, medical, and industrial applications. The industry needs to focus more on innovation and the development of specialised products to expand its market reach.
Geopolitical factors: Geopolitical uncertainties, such as trade wars, tariffs, and regional tensions, can disrupt supply chains and limit market access. The global textile industry is highly integrated, and any trade restrictions or changes in international trade policies could have a direct impact on Indian exports.
Slow adoption of technology: Although there have been improvements in automation, AI, and digitalisation in the textile industry, the pace of technology adoption has been slow in some areas. Companies will need to invest in modern technologies to increase productivity, improve product quality, and reduce costs. The industry as a whole need to embrace Industry 4.0 to stay competitive globally.
While the target of $350 billion is achievable, India’s textile industry will need to overcome these significant challenges by embracing innovation, improving sustainability practices, addressing skill gaps, and investing in modern infrastructure to fully realise its growth potential.
How important is technological modernisation for enhancing the Indian T&A industry’s global competitiveness? What more can be done to accelerate the adoption of cutting-edge technologies in this sector?
Technological modernisation is absolutely vital for enhancing the Indian textile sector’s global competitiveness. Embracing automation, AI, sustainable technologies, and digitalisation will not only improve efficiency and quality but also allow Indian companies to access new markets and adapt to evolving consumer preferences. To accelerate the adoption of these technologies, the government, private sector, and educational institutions must collaborate closely to overcome financial, skill, and infrastructure barriers, ensuring the industry is equipped for a sustainable, high-tech future.
What opportunities do you foresee for your company as the Indian T&As industry aims to achieve their 2030 target?
Moksha Thermoplastics, established in 1954, specialises in manufacturing high-quality yarn carriers such as roving bobbins, Ring spinning tubes, Yarn winding and Yarn dyeing cones and cheeses.
As the Indian textile industry targets high in exports by 2030, Moksha Thermoplastics is well-positioned to contribute to this ambitious goal. By leveraging its technological capabilities and aligning with the strategic objectives of the Indian textile industry, Moksha Thermoplastics can play a pivotal role in achieving the 2030 export target.
With the need for sustainability growing in the T&As industry, how is your company helping T&A makers to achieve their green goals?
Moksha Thermoplastics is actively supporting the textile spinning industry in its pursuit of sustainability by developing innovative yarn carriers that enhance production efficiency and reduce environmental impact.
Slim Line Tubes: Moksha has introduced the Moksha Slim Line i.v. Ring Tubes, which are only 1.5 mm thick. These are among the world’s slimmest thermoplastic tubes, successfully operating across the entire spinning production for cotton to polyester yarns. The reduced material usage in these tubes contributes to resource conservation.
Through these initiatives, Moksha Thermoplastics is enabling textile manufacturers to achieve their green goals by providing products that enhance efficiency, reduce waste, and support sustainable production processes.
What measures should the government take to further strengthen the Indian T&As and TMA industries?
To strengthen India’s textile and machinery industries, the government can take several measures:
- Increase financial support: Boost schemes like the PLI to encourage investment in modern machinery and technology.
- Develop Infrastructure: Focus on textile parks, logistics hubs, and R&D centres for better production efficiency.
- Enhance skill development: Launch programs to improve the workforce’s skills and quality.
- Trade policy reforms: Reduce tariffs and negotiate favourable trade agreements to make Indian textiles more competitive.
- Promote sustainability: Encourage eco-friendly manufacturing to appeal to global consumers.
- Support research and innovation: Offer grants to foster innovation in products and processes.
- Strengthen export promotion: Provide incentives and marketing support for export-oriented units to expand market reach.
These actions will help make India’s textile industry more competitive globally.
What are emerging trends in the textile machinery & accessories industry?
The textile machinery and accessories industry is evolving rapidly, driven by technological advancements and shifting market demands. Key emerging trends include:
- Digitalisation and automation: The integration of Internet of Things (IoT), Artificial Intelligence (AI), and data analytics is transforming manufacturing processes. These technologies enable real-time monitoring, predictive maintenance, and enhanced operational efficiency.
- Sustainability initiatives: There is a growing emphasis on sustainable practices, such as the development of biodegradable fabrics and the adoption of circular economy models. These approaches aim to reduce waste and conserve resources.
- Customisation and personalisation: Advancements in 3D printing and digital printing technologies allow for on-demand manufacturing and personalised designs, catering to consumer preferences for unique and customised products.
- Smart textiles: The development of textiles that respond to external stimuli—such as heat, light, or moisture—is gaining momentum. These smart textiles have applications in medical, sports, and fashion industries, offering functionalities like health monitoring and environmental adaptability.
- Advanced robotics: The use of robotics in textile manufacturing is increasing, with applications in automated sewing, quality inspection, and material handling, leading to improved productivity and consistency.
- Blockchain technology: Blockchain is being explored to enhance supply chain transparency, ensuring ethical sourcing and product authenticity, which is increasingly important to consumers.
These trends reflect a shift towards more efficient, sustainable, and consumer-centric practices in the textile machinery and accessories industry.
What are your growth plans in the next two years?
Moksha Thermoplastics, specialises in manufacturing high-quality yarn carriers for the textile industry. Over the next two years, the company plans to focus on strategic growth and innovation across multiple areas. The company aims to expand its product line by introducing new offerings, such as innovatively designed card cans with simplified operations and precise functionality. Efforts are also being made to enhance automation in production processes, ensuring compatibility with advanced systems to improve overall efficiency. Collaboration with machinery manufacturers remains a priority to develop new designs and features that enhance product utility and performance. Additionally, Moksha plans to strengthen its global presence by increasing exports, which currently account for approximately 20 per cent of production, primarily to Asian and African markets. To support this growth and innovation, the company continues to invest in state-of-the-art infrastructure, including a modern injection moulding plant and an in-house tool room.