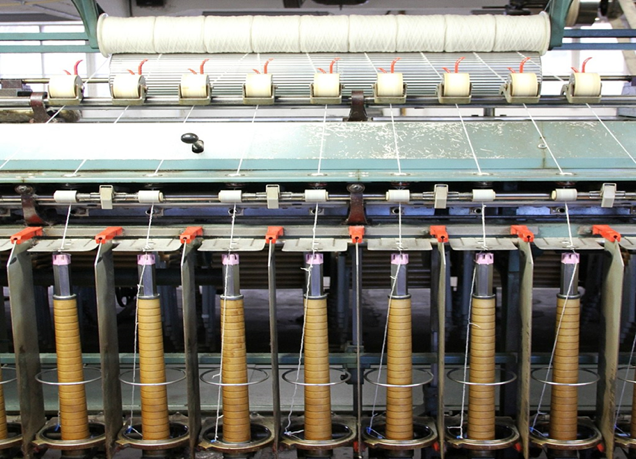
Air compressors in the textile industry and their efficiency
What exactly is the function of compressed air in this fast-advancing industry that is so significant for the economy? And is this power source cost-effective…
While compressors are used in almost all industries, the textile industry definitely takes the cake. In both man-made and natural textile production, compressed air plays a key role at every stage.
But what exactly is the function of compressed air in this fast-advancing industry that is so significant for the economy? And is this power source cost-effective?
Compressed air’s role in the textile industry
To an outsider, reliable compressed air may not seem like a major requirement in the textile industry. However, it’s a necessity at almost all levels of the supply chain, one that can make the difference between fast and effective processing in this competitive industry. Compressed air:
- Powers air-jet looms, spinning machines, ginning mills and other industrial equipment used to process denim, polyester yarns and other fabrics.
- Adds texture to fabrics and other details that increase the value of your finished product.
- Powers tools that keep facilities clean and equipment working its best.
As the industry continues to evolve, textile manufacturers will keep looking for ways to improve the efficiency of their processes with new equipment.
Industry challenges and opportunities
What role compressed air will play in the textile industry of the future will depend on the availability and effectiveness of sophisticated machinery that helps manufacturers overcome some of their most persistent challenges. These include:
- Reducing costs associated with operating and maintaining compressed air tools and systems
- Maximising uptime and productivity to meet the demands of customers
- Preventing contamination due to air/fluid mixture
- Reducing waste and running a more sustainable operation overall
- Retrofitting aging production centres with modern equipment
With the right equipment, even the most difficult challenges can be turned into a profit-generating opportunity. Quincy’s air compressors for the textile industry offer a number of competitive advantages. With our products, you’ll gain efficiency and reliability to run a more streamlined and cost-effective operation, work faster in cleaner environments, and reduce your reliance on fossil fuels through energy-efficient technology.
Energy consumption of chosen spinning mill
In order to obtain the necessary information about energy consumption of a specific spinning mill, one which is able to spin every kind of staple fibre (i.e. cotton, linen, polyester, viscose) in a wide count range using both ring and open-end systems to be chosen.
Energy consumption of a month for a chosen spinning mill
The chosen spinning mill operated in 3 shifts a day which consisted of 8 hours and also works 25 days a month. Considering the monthly operating time and number of machines, the monthly energy consumption of the chosen spinning mill was calculated and all the data are shown in the following table. The actual total monthly energy consumption of the spinning mill was 1459680 kWh/month as shown. 78.4% of this energy was consumed by the machines, and 37% of the monthly energy consumed by the machines was due to the ring-spinning machines.
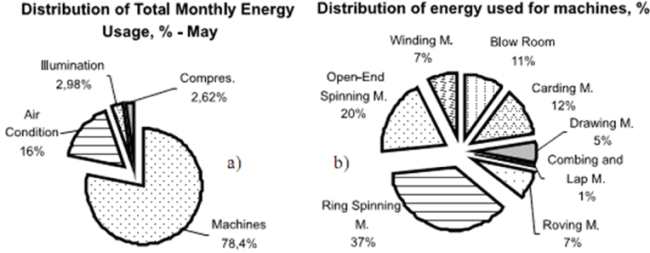
Source: rastgar-co.com