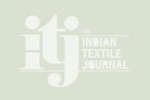
Accuracy of yarn count measurement put to test
Total transparency and accuracy in yarn count is regarded as one of the most crucial quality parameters for yarn trading and yarn processing. Even the slightest variations in yarn count can cause serious fabric defects such as striping, ruining the finished product. So, it’s obvious that control of this parameter is important. Any control is better than none at all, and standard manual methods fall into this category. Automatic measurement of absolute yarn count – and its variations – is therefore much faster, reliable and easier, using the Sensor FA with the USTER® TESTER 6. But how accurate is this high-speed solution? Detailed testing regimes at two spinning mills, in Europe and the USA, provided the answer.
Sensor FA of the USTER TESTER 6 undergoes exhaustive mill trials.
Total transparency and accuracy in yarn count is regarded as one of the most crucial quality parameters for yarn trading and yarn processing. Even the slightest variations in yarn count can cause serious fabric defects such as striping, ruining the finished product. So, it’s obvious that control of this parameter is important. Any control is better than none at all, and standard manual methods fall into this category. Automatic measurement of absolute yarn count – and its variations – is therefore much faster, reliable and easier, using the Sensor FA with the USTER® TESTER 6. But how accurate is this high-speed solution? Detailed testing regimes at two spinning mills, in Europe and the USA, provided the answer.
Marketing of yarns requires careful control of the same three success factors as for any other product area: sourcing, costs and quality. When it comes to quality, yarn count is the key parameter which can make or break a successful deal, so spinners need to pay close attention to reliable monitoring of any potentially damaging variations.
The classic manual method of count measurement requires two instruments: a yarn reel and a balance.
The procedure is slow, labor-intensive and subject to human error. The automatic option, using the USTER® TESTER 6 with the Sensor FA for automatic fineness, is fast – with testing speeds of 800 m/min. It also needs only one operator and there is no risk of human error. These advantages of automatic count measurement are immense, but the accuracy of the results is the all-important issue. This was the challenge taken up at two spinning mills.
“It is only to be expected that the test results for a crucial quality parameter such as yarn count will be questioned closely,†says Wolfram Soell, Textile Technologist within Uster Technologies, who executed the trial on the accuracy of the USTER® TESTER 6 in a spinning mill in Europe.
This customer has a reference yarn, which was tested every week for a long-term observation of the yarn count accuracy in the mill’s laboratory. The trial ran from January to August 2017, and during the first month the tests were carried out at speeds of both 400 m/min and 800 m/min. It was quickly seen that the measurement results were independent of the testing speed, so the tests continued only at 800 m/min. During the testing period, results for the 100 per cent combed cotton Ne 30 ring yarn showed minimal variation. On the graph with data for the absolute count the red line indicates the insignificant variation from tex 19.82 (Ne 29.8) to tex 20.14 (Ne 29.3).
Expert analysis of these results demonstrated the excellent accuracy of the Sensor FA for yarn count measurement. The ideal proof of its reliable accuracy, however, would come from a direct comparison with the standard manual method.
This was organised when a US customer initiated a trial after a new USTER® TESTER 6 installation, measuring 32 different yarns with five packages each over a four-week period. “In a pre-test of 13 samples, the Sensor FA averaged Ne 0.1 counts heavier than the standard count determination method. When repeating the test the average count was Ne 0.1 lighter. So overall the two methods were extremely close,†says Raul Thomas, Textile Lab and Training Manager within the USTER subsidiary based in North Carolina. Thomas is familiar with the detailed conditions in this mill and knows that data for these tests was taken from cones as well as from bobbins. With respect to count variation, the Sensor FA had much lower variation than the standard method in almost every test.
All the parties involved were well satisfied with the conduct and outcome of these trials. To USTER, it was gratifying that feedback from customers was very positive regarding the ease of use. The spinners in the trials appreciated the integration of international standards for selection of the predefined yarn length for the tests. This ensured the most accurate yarn count determination, without error-prone human interaction, while also giving the option of customised setting of the predefined yarn length. The USTER® STATISTICS worldwide benchmarks also provide enhanced and built-in knowledge for the automatic comparison of yarn count variations.
With the USTER® TESTER 6, the FA measurement is carried out simultaneously with other measurements such as evenness, imperfection and hairiness. Consequently, the yarn count tests are based on a large number of measurements, giving even greater precision. Passing this extensive double challenge, the Sensor FA can provide spinners and their customers with the ultimate guarantee of optimum fabric appearance. The Uster Group is the leading high-technology instrument manufacturer of products for quality measurement and certification for the textile industry. The Group provides testing and monitoring instruments, systems and services that allow optimisation of quality through each individual stage of textile production.
This includes raw textile fibers, such as cotton or wool, all staple fiber and filament yarns, as well as downstream services to the final finished fabric. The Uster Group provides benchmarks that are a basis for the trading of textile products at assured levels of quality across global markets. The Group’s aim is to forward know-how on quality, productivity and cost to the textile industry.