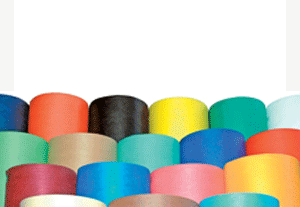
A critical analysis of nonwoven technologies
Nonwoven fabrics have quietly revolutionised consumer, medical, and industrial market places, say Laga S K, Vignesh Dhanabalan and Daniel Karthik who provide details of the manufacturing of nonwoven with emphasis on fibre usage,
Nonwoven fabrics have quietly revolutionised consumer, medical, and industrial market places, say Laga S K, Vignesh Dhanabalan and Daniel Karthik who provide details of the manufacturing of nonwoven with emphasis on fibre usage, web laying technologies, and conversion of webs into fabrics.
Nonwoven is an engineered fabric structure made directly from fibres, to provide specific function to ensure fitness for purpose. The term "nonwoven" is often used as a generic description of a fabric that is not produced by process of weaving or knitting, more broadly, a fabric that is different from a traditional textile fabric. Like textile fabrics, nonwoven is a planar structure that is produced with varying degrees of integrity, surface texture, thickness, flexibility, and porosity that involves low cost and production process.
In fact, the technologies used to make nonwoven fabrics are based on fundamental principles used to produce textiles, papers, and plastics. In this regard, nonwovens are fabrics that are made by mechanically, chemically, or thermally interlocking layers or networks of fibres or filaments or yarns.
In spite of this mass-production approach, the nonwovens industry produces a wide range of fabric properties from open wadding suitable for insulation containing only 2-3 per cent fibres by volume to stiff reinforcing fabrics where the fibre content may be over 80 per cent by volume. One of the major advantages of nonwoven manufacturing is that, it is generally done in one continuous process directly from the raw material to the finished fabric. When compared to other fabric manufacturing techniques nonwoven technique is found to be the best in terms of production ratio.
Raw materials & their properties
The end use of materials has been the driving force for the development of products and technology. Raw material is the key factor in designing of material, and the selection of raw material affects the function and quality of the product. The manufacturing processes for non-woven fabrics invariably consists of two distinct phases, web formation, followed by subsequent bonding.
Web formation
Dry laid process: In dry laid process, web is produced from staple fibres. These fibres are directly laid from a carding machine to form the matt ranging from 10-2,500 gsm. The carding machine used is not the regular ones they are equipped with worker and stripper rollers. There are three methods for dry lying of web.
Parallel laying: The mass per unit area of card web is normally too low to be used directly in a nonwoven. They are increased by laying several card webs one over the other to form the matt. The simplest and cheapest way of doing this is by parallel lying. Figure 1 shows five cards raised slightly above the floor to allow a long conveyor lattice to pass underneath. The webs from each card fall onto the lattice forming a matt with five times the mass per unit area.
Cross laying: In cross laying, the cards (or cards) are placed at right angles to the main conveyor as shown in Figure 2. In this case the card web is traversed backwards and forwards across the main conveyor resulting is a zig-zag motion as shown in Figure 2
Air laying: The air-laying method produces the final matt in one stage without first making the intermediate lighter weight web. It is capable of running at high production speeds but is similar to the parallel-lay method. The width of the final matt is the same as the width of the air-laying machine, usually in the range of 3û4 m. Opened fibre from the opening/blending section is fed into the back of hopper (A), which delivers a uniform sheet of fibres to the feed rollers. The fibre is then taken by the toothed roller (B), which is revolving at high speed. The worker and stripper rollers set to the roller (B) to improve the opening p