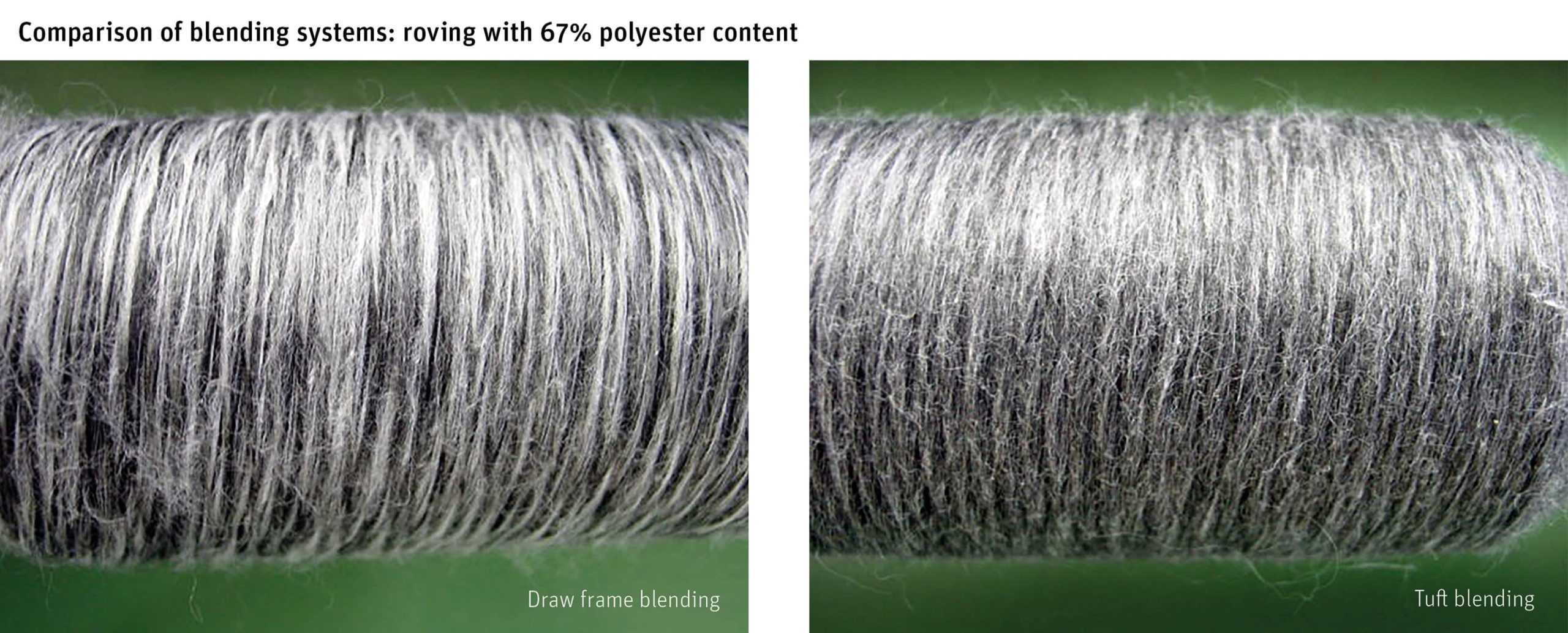
Two blending systems for different requirements
Estimates suggest that 45% of short-staple fibres are processed in their pure state, while 55% are spun into blended yarns. Cotton and polyester blends are the most popular type of blended yarn. Due to the increasing consumption of man-made fibres and the important role of blends, Rieter has conducted research into the influence of different blending systems on intermediate and end products.
Blended yarns are so appealing because the yarn properties can be specifically influenced through the combination of fibres made of different raw materials or of varying length or fineness. A business shirt has different requirements in terms of yarn than a pair of hiking pants or a sports shirt. Blending can take place at different process steps in the spinning process – during fibre preparation or on the draw frame. How does this affect the sliver, the yarn, and the textile surface?
To answer this, Rieter has developed a guideline that analyses when each blending system is most suitable, taking into account the end spinning process and varying polyester content.
Tuft or draw frame blending
Two common blending systems are used in spinning mills. First, there is tuft blending: This involves raw material being continuously fed in during fibre preparation via the precision blender UNIblend. Second, there is draw frame blending, which involves card sliver from each of the raw-material components being blended on the draw frame. To find out which blending system is recommended, ring and rotor yarn was produced and the intermediate products, the yarn and the fabrics were examined based on various quality criteria. A medium-quality cotton and a spun-dyed polyester (black) were selected as raw materials for the research. Using the color difference between the fibres, it is possible to assess the blending behavior even at the beginning of the process steps.
The entire system influences the blend
In the case of tuft blending, the blending begins earlier in the spinning process, whereas with draw frame blending it takes place later. However, the research has shown that the entire system, not just a single process step, has an influence on the blend. The card, the draw frame passages, and the end spinning machine perform part of the blending process and therefore have an impact on homogeneity.
Tuft blending creates improved homogeneity for ring yarn
In comparison to the rotor spinning machine, less fiber blending occurs on the ring spinning machine. It is therefore important that the blending of the fibers begins as early as possible in the process. For this reason, tuft blending is the more suitable choice for ring yarns compared to draw frame blending. Here, the continuous fiber feed provided by the UNIblend ensures better homogeneity (Fig 1). By far the best blend consistency is achieved by means of tuft blending with two draw frame passages (Fig 2).
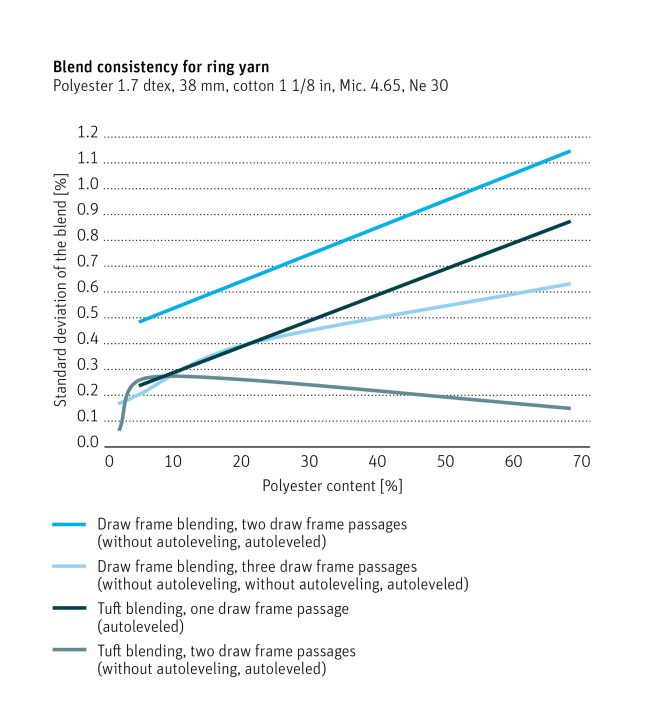
Fig 2: Tuft blending with two draw frame passages generates the best results for ring yarn.
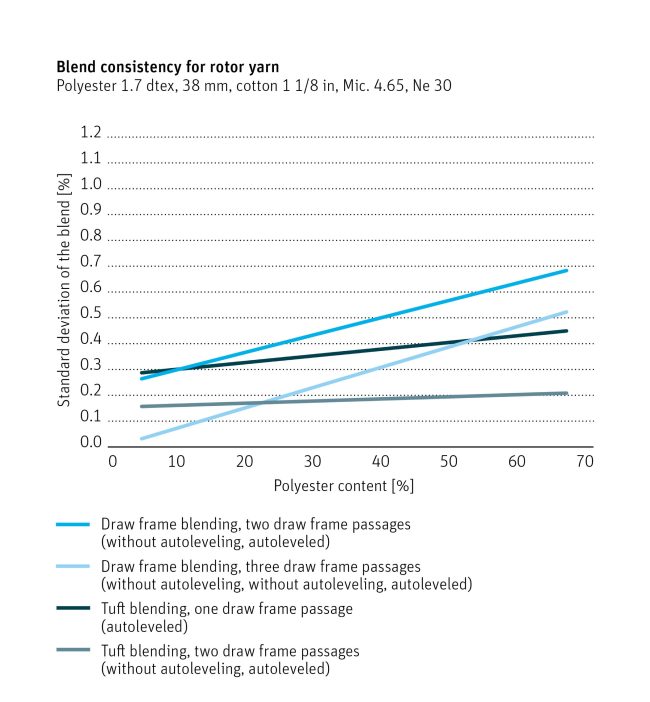
Fig 3: In rotor spinning, the blending system and the polyester content play a less important role.
Additional blending effect in rotor spinning
With rotor spinning, the opening into single fibers by the opening roller and the fiber doubling in the rotor has an additional effect on fiber blending. As a result, the blending method has less influence on rotor yarn (Fig 3) and, from a technological point of view, draw frame blending is suitable in many cases. Generally, two draw frame passages are sufficient to achieve a consistent blend.
Influence of the blending ratio
Polyester has a higher tenacity than cotton. This is one reason why this fiber blend is so popular. The percentage of polyester has a greater influence on the yarn properties of ring yarn than on rotor yarn. This is due to the different yarn structure. As the polyester content increases, so too does both the yarn tenacity and evenness. The blending consistency, however, decreases.
Rieter is the world’s leading supplier of systems for short-staple fiber spinning. Based in Winterthur (Switzerland), the company develops and manufactures machinery, systems and components used to convert natural and man-made fibers and their blends into yarns. Rieter is the only supplier worldwide to cover both spinning preparation processes and all four end-spinning processes currently established on the market. Furthermore, Rieter is a leader in the field of precision winding machines. With 17 manufacturing locations in ten countries, the company employs a global workforce of some 4 900, about 18% of whom are based in Switzerland.