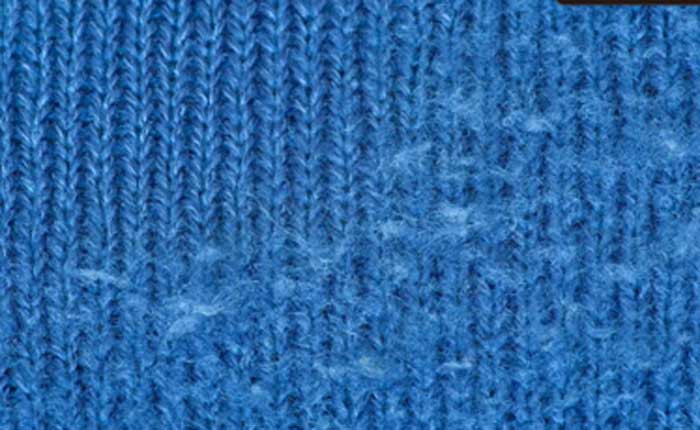
Pills Free Textiles
Antipilling offers an enhanced appearance and improved durability while maintaining its softness and comfort, informs Dr Ashok Athalye
The pilling of apparel clothing and home decor fabrics is a major concern and a value eroder. Consumers pay a premium for garments and upholstery that exude elegance, comfort, and lasting quality. However, even the most esteemed manufacturers face a persistent enemy – the pilling of fibres. Pills are the little balls of fibre that erupt on the fabric surface, which not only spoils the garment’s luxurious feel but also undermines its intended value. Pilling is also known as fuzzing and refers to the accumulation of tangled fibres on the fabric surface, which gives the garment an unsightly and worn-out appearance.
Cause of pilling
The process and progress of pilling is a complex phenomenon and needs careful understanding of various aspects which lead to pill formation.
Wear and tear: The garment user’s physical movements, like walking, sitting, stretching, etc., create friction against clothing. This constant rubbing loosens and breaks individual fibres on the fabric’s surface. These loose fibres then tangle and clump together, forming the visible pills.
Washing and rubbing: Washing of textiles is essential for keeping the clothes clean, however, during the washing process, the tumbling action in the washing machine, along with the rubbing against other garments, creates friction that accelerates fibre breakage and pilling. Additionally, harsh detergents or high drying temperatures can further weaken fibres, making them more prone to pilling.
Mechanism of pilling
Loosening: The friction caused during garment wear, washing, or rubbing against other surfaces loosens out the fibres, which get pulled out like tiny hairs poking out from the fabric’s smooth surface.
Entanglement: When theloose fibres continue to experience friction, they become more susceptible to snagging and tangling with each other.
Ball formation: With continued friction, the tangled fibres become compact and get compressed, forming a tight, round ball, this is called fibre-pill. This pill remains anchored to the fabric surface by other partially broken fibres, making it difficult to detach or remove.

Figure 1: Mechanism of pilling
Types of pilling
- Mild – slight fuzziness on the fabric surface
- Moderate – fabric surface is randomly covered in pills of different sizes and densities
- High – significant surface area is covered with pills of varying sizes and densities
- Severe – pilling that covers the entire surface of the fabric
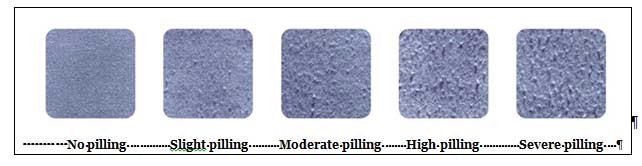
Figure 2: Types of pilling
Reasons of pilling
Type of fibre: Synthetic fabrics tend to form pills that are very tough to remove. Picking at them can snag the fabric and create more problems. Natural fibres, on the other hand, pill more easily, but the pills are also much easier to remove.
Length of fibre: Fabrics made from smaller/shorter fibres tend to pill more because they’re more likely to snag and break loose with wear. On the other hand, longer fibres are more resistant to friction and hold together better, reducing the chance of pilling.
Type of yarn: High twist and tighter/compact yarns are less likely to pill. Loose yarns, with fewer twists, are more prone to pilling. The combed fibre yarns are less likely to pill than the carded one.
Composition of fabric: Blended fabric, having amix of different fibres in varying ratios tends to increase the severity of pilling. When one fibre (man-made) is much stronger than the other (Natural), the weaker fibres break easily and form little balls of fuzz (pills) that get stuck on the stronger fibres. This makes the pilling more noticeable and difficult to remove.
Structure of fabric: Loosely knit fabrics, like sweaters, are more likely to pill because the fibres can snag and break free more easily. On the other hand, tightly woven fabrics or those made with strong, twisted yarns hold their fibers together better.
Methods of anti-pilling
Antipilling chemicals help reduce or overc
ome the formation of pills. There are two types of antipilling agents used in the textile industry:
- Yarn lubricants: These polymeric chemicals reduce fibre friction and prevent them from breaking, detaching, and entangling to form pills. Silicone-based compounds are commonly used lubricating antipilling agents.
- Film formers: These chemicals create a thin, protective layer on the fibre surface, which prevents loose fibres from breaking off. They also smoothen the fibre surface, reducing fibre breakage due to abrasion. Polyurethanes, acrylic resins, and some fluorocarbons are examples of film-forming antipilling agents.
Evaluation of pilling
Different test methods are used to evaluate the anti-pilling performance depending on the end-use requirement of the fabric. Given below are three of the most common ones
- Martindale abrasion tester: Here, the fabric samples are rubbed against a standard abrasive surface or another fabric sample under controlled pressure and speed for a set number of cycles. After the test, the degree of pilling formation is visually assessed using a standardised grading scale.
- ICI pilling tester: This method simulates the tumbling action fabrics experience during wear and washing. Fabric samples are placed in a cork-lined box with a tumbling mechanism. After specified revolutions, the samples are visually inspected for pilling formation.
- Random tumble tester: This method utilises a rotating drum to simulate the tumbling action fabrics experience in a washing machine. Fabric samples, along with some cotton lint (to mimic fibre shedding), are placed inside the drum and tumbled for a set duration. The level of pilling is then visually assessed.
These tests provide a standardised way to compare the anti-pilling performance of different fabrics or fabrics treated with various anti-pilling agents. The specific test method chosen will depend on the type of fabric being tested and the desired information.
Benefits of antipilling
Antipilling offers an enhanced appearance and improved durability while maintaining its softness and comfort. These features contribute to increased consumer satisfaction.
Acknowledgement
The author wishes to acknowledge the Department of Fibres and Textile Processing Technology, Institute of Chemical Technology, Mumbai and Rossari Biotech for contributing relevant information.
About the author:
Dr Ashok Athalye is a Professor of Textile Chemistry and Vice-President of Technological Association (ICT- Mumbai), Fellow of the Society of Dyers and Colourists (FSDC-UK) and Fellow of the Indian Chemical Society (FICS).