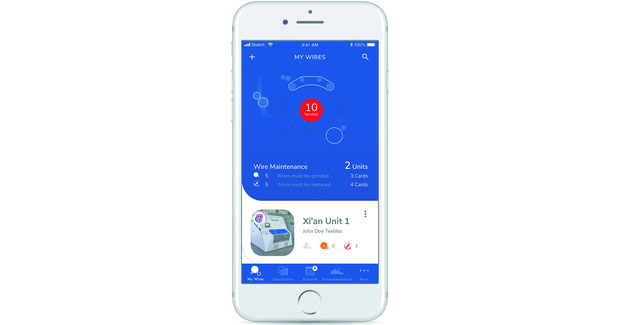
Truetzschler solutions for spinning preparation, nonwovens & MMF
Cost pressure, personnel bottlenecks and fluctuating raw material qualities: These are some of the most pressing challenges in spinning preparation. At the same time, spinning preparation is decisive for the yarn’s quality.
Cost pressure, personnel bottlenecks and fluctuating raw material qualities: These are some of the most pressing challenges in spinning preparation. At the same time, spinning preparation is decisive for the yarn’s quality. In order to meet these requirements, Truetzschler counts on state-of-the-art sensor technology and digital integration – and opens up a new chapter in carding technology: The new intelligent card TC 19i automatically and continuously optimises the carding gap whose setting has a critical influence on quality and performance. With a precision not achievable by humans, the intelligent card permanently realizes even the narrowest carding gap setting of 3/1000 inch. “This allows us to measurably improve our customers’ raw material utilisation and productivity while achieving consistently high quality," says Dr Dirk Burger, CEO of the Truetzschler Group.
In addition, new cloud-based digital monitoring and management systems provide yarn manufacturers with transparency over all processes in the spinning mill. The My Wires app, for example, provides information on the status of clothings and service intervals and helps with the planning of reorders. Competent service for re-clothing can be provided immediately by Truetzschler Card Clothing (TCC). “With the smart networking of machines as well as production and maintenance, we support customers in simplifying their entire spinning process,†explains Dr Christof Soest, CTO of the Truetzschler Group, and emphasises: “This is why our digital platforms work not only for Truetzschler technology.â€
The latest innovation in the blowroom offers more economy and quality as well: The Portal Bale Opener BO-P, with widths of 2,900 mm or 3,500 mm, allows significantly more bales to be placed side by side and processes them in parallel using two opening rolls. Thus, it results in significantly better blending and higher productions of up to 3,000 kg/h.
Read full story in ITJ Supplement
CATEGORIES Industry Update