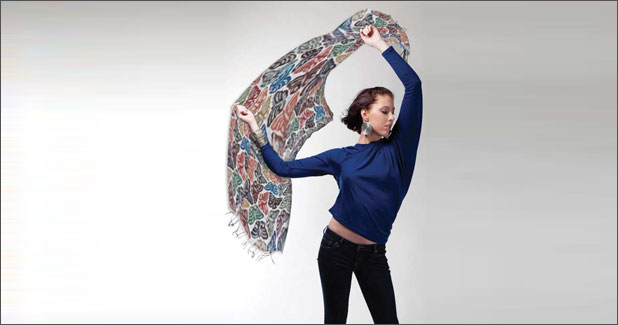
Software used in textile design
Textile industries face significant challenges to remain competitive in today’s industry, supplying innovative collections at right price, controlling margins, building customer loyalty and expanding business horizons, says Sneha Ishwar Vaghela.
Textile industries face significant challenges to remain competitive in today’s industry, supplying innovative collections at right price, controlling margins, building customer loyalty and expanding business horizons, says Sneha Ishwar Vaghela.
Textile design is the process of planning and producing a fabric’s appearance and structure. Textile designers dream up designs that are woven or knitted into cloth or printed on fabric. They might suggest types of thread to weave together for a specific look and feel or create patterns that adorn a fabric surface. Textile designers might also specify a dyeing method, or the use of dyes to colour fibres or fabric surfaces to achieve a desired effect. Textile designers are involved with the production of these designs, which are used, sometimes repetitively, in clothing and interior decor items. The field encompasses the actual pattern making while supervising the production process. In other words, textile design is a process from the raw material into finished product. Fibre, yarn and finishes are the key elements to be considered during the textile design procedure. There are two important elements from the textile design tradition that will play a role in our further studies of textiles. One is related to the division of labour and the other to the design variable at play in the practical process of design.
The experts in textile design procedure
The technology of artificial intelligence (AI) and expert system (ES) enables computers to be applied to less determined design tasks, which require symbolic manipulation and reasoning instead of routine processing. ES can be used to diagnose, repair, monitor, analyse, consult, plan, design, instruct, explain, learn and conceptualise problems. ES provide powerful tools for solving problems such as design and are very suitable for database manipulation and decision making.
Knit CAD: In addition to the generic CAD software applicable to all designers, it also has specialist CAD packages for knitwear designers. This software enables designs to be developed and knitting instructions to be sent to the knitting machines to control production.
The software also allows designs to be simulated in 3D and printed.
Weave CAD: This is specialist ‘Scotweave’ software that enables the development of complex weave structures. The software simulates the structure and also produces peg plans and lifting plans for the designer simplifying the weave process and helping to guarantee the intended result.
Fashion CAD: The fashion CAD suite is specifically dedicated to fashion design, pattern making, lay planning and fashion production. It contains: Adobe CS5 suite, Lectra, Kaledo Style illustration software, Modaris pattern drafting, modification and grading software, Diamino marker planning and fabric utilisation software, two large format digitisers and one large format pattern plotter.
Print CAD: Most of print designers routinely use Adobe Photoshop and/or Adobe Illustrator to develop their images. These images may then be fed directly to the digital printer if appropriate. When the designer wishes to screen print their images (or part of their images) they will often use the ‘studio master’ software for separating and preparing their screens.
Software for yarn
Artificial neutral network (ANN): The use of artificial neural networks (ANNs) to develop a model of the relation between physical structure and mechanical properties of constituent fibres, but also yarn structure characterised by geometric arrangement of fibres in the yarn body. Although there are many studies related to analysing the migratory properties of spun yarn, there are no study available about predicting yarn migration parameters. The prediction by using intelligent technique of artificial neutral network (ANN).
Electronic Inspection Board – Hairiness Tester: The spun yarn uniformity has always been an important quality control parameter as it affects the commercial value of the yarn. Defects such as thick places, thin places, neps, hairiness and yarn appearance contribute to the overall yarn uniformity and altogether they define the character of the end product. The Electronic Inspection Board for Spun Yarns and Hairiness, EIB-S is a test instrument, which offers very quick, precise yarn analysis based on the yarn diameter measurements.
A CCD camera is used to measure the diameter values with 3.25 micron precision when the yarn is moving at test speeds up to 300 m/min. The unique camera design provides the ability to test natural and synthetic yarns as well as high performance yarns including carbon, glass or hybrid yarns that cannot be tested with capacitive based systems. Yarn Analysis Software (YAS) measures the yarn diameter and classifies the yarn defects such as thick places, thin places, neps and slubs by their diameter and length.
The programme provides the best simulated yarn appearance board in the market. The flexibility included in YAS software allows the operator to change board length and yarn fault descriptions without retesting the yarn. This allows the user to evaluate the same yarn at different loom widths to see if any periodicity develops. Diameter data can also be exported to a fabric simulation software for further analysis.
Features include:
Software for fabric (weaving)
Computer Aided Dobby Design: Today, the textile designers have to be more productive and creative due to the dynamic textile market. For this, a computer-based interactive textile designing and sample weaving system is highly beneficial to the designer. Computer-aided designs enable the textile designer to conceive better and more patterns to suit the requirement and liking of the customers. This could not have been possible to a great extent if the same patterns were to be produced by the conventional method of designing. According to the oxford dictionary, dobby is defined as “A mechanism connected to a loom for weaving small patterns similar to but simpler than those produced by a Jacquard loomâ€. The first dobby/jacquard was invented by Joseph Marie. Although, mechanical dobby system did not have a programmable device but it played an important role in textile industry. With dobby design, designers can concentrate on the finer aspects of their creations without getting into machine specific details like color values, codes and other technicalities Dobby design offers a comprehensive and efficient user interface that allows users to specify, construct, visualise, and execute designs in real time. It can automatically insert weave structures at specific areas, add desirable warp and weft structures to your textile designs, and integrate colors as per your loom.
Textronics: Design dobby offers the best woven fabric simulation available in the market today. The simulation module brings the very complex process of dobby weaving to life on a computer screen or printout. Control functions such as reed, draw-in, and warp and weft sequences are taken into account in the simulation just as yarn properties, yarn material, and yarn colours are. Analysing all these parameters that are automatically included in the design file from the editing process in the dobby main module to the dynamic behaviour and the paths of all thread systems is determined and then corrected according to their real appearance. The image file generated is then displayed and may then be printed out. Simulation differentiates between the front and back of the fabric.
The dobby design provides:
They are more stable and stretchy compared to fabrics made through basic weaves. Atlases fabric, satin fabrics, brocade fabric, and damask fabric are some of the examples of jacquard fabric. Computer-aided textile designing software helps the designer to design in the graph either directly or through scanner and digitiser. CAD software is useful for jacquard, dobby and treadle designing.
The pixel graph designs can be transferred either to floppy or taken as graph print out using printer. The data punched floppy directly operates the needle of the fine pitch electronic jacquard The different CAD software are Texnronics, wonder weaves, CADantage, Autotex, Texgraphics and Ned graphics. Electronic jacquards are directly operated by data formatted from computer. Hence, for the electronic jacquard the graph remains in the computer and there is no any virtual graph paper. Similarly, there are no punch cards required to be punched using punching machines. After graph designing in the computer, the design is transferred into the floppy. The floppy is feed to the fulli automatic punching machines. Card feeling is done automatically. As per the marks and blanks of the designs in the floppy, the electronic head stock with punches of the machine punches the card automatically. The speed is 80 to 120 cards per hour (240 hooks) The punched cards are locked and used in the mechanical jacquard of handloom or powerloom. The advantages is error free punching of designs in the card from the data formatted floppy. CAD benefits: The textile designs are the original works of the designers. Cad helps them to visualise and see their imaginative design in final form without producing any sample swatch. Sometimes, the customers to provide ideas for designing according to their particular requirement. These are in the form of painted artwork or fabric samples and sometimes film negatives. The textile designers, with the help of cad, convert them into workable designs. For this to be done, the sample is scanned with the help of either scanners or digital cameras and then they are edited to obtain the final design.
The usefulness of CAD has driven the market to produce specific softwares for different aspects of textile and apparel manufacturing. If there are softwares for designing footwear, caps and bags, there are pattern making software for fashion industry. There are solutions for sewn goods industry as well as systems for the design of jacquard woven fabrics. The garment pattern designs are even available in home, expert, and professional versions. Precision cutting systems, cutting and plotting systems, pattern design, grading and marker making- you name it and there is software for every textile related work- this is IT revolution in textile industry.
CAD has many advantages:
WeaveIt: Weave it is a weaving software programme for creating, designing and displaying weaving drafts and patterns. Weavers create the threading, treadling and tie-up and WeaveIt will display the draft as a drawdown. iWeaveit: iWeaveIt for tablets and phones is available on both the Apple IOS and the Android systems. iWeaveIt app is a basic drawdown programme. Weavers can create and edit the threading, treadling and tie-up – iWeaveIt reads and writes WIF files. Internet files and emailed files can be imported with only one click.
Grid ‘n Weaveit: Grid ‘n WeaveIt provides basic drawing tools. It allows you to specify the weaving properties of the drawing based on warps and yarns. You can create a grid that prints over the drawing to help size you’re weaving.
Arahweave: Weave up to 32,000 x 32,000 ends/picks, graphical browsing of fabrics, weaves, images, warp/weft patterns, jacquard cards, superior on-line simulation in real 1:1 size and density, warp or weft pattern on the simulation with mouse, and more.
licTexPro: Versatile CAD for fashion and textiles. Create exciting artwork, fabric colourways, storyboards plus knit & weave simulations.
Software for apparel design
Adobe Illustrator: Adobe Illustrator Adobe enables students, photographers, and small to medium businesses to create beautiful clothing designs with easy access to all your favorite assets, including images, colors, brushes, and type styles.
C-design fashion: Allows you to create ready-to-wear collections and to release your technical files quickly and efficiently
Vetigraph: It gives CAD/CAM solutions for apparel and fashion grade patterns, plotters for markers, automatic cutting machines and fashion.
Zedonk software: Zedonk is an affordable, online apparel and production inventory management software system for designers and makers of clothing, footwear, jewelry and accessories. Also launched is an iPad. CorelDraw: It is a professional graphic design software to help you quickly and easily create modern fashion designs. Includes thousands of high-quality images, fonts, and templates.
Software for garment
Virtual product development (VPD) is the practices of developing and prototyping products in a completely digital 2D/3D environment. VPD has four main components:
Virtual garment simulation: The simulation is a reality imitation. Clothing manufacturers require systems with the capacity to deal with garment design process as a whole, including possibilities to work directly within a 3D graphic environment. In such a context, the aim of the author’s research work has been the development of a graphic and interactive environment to design men garments and simulate their behaviour according to fabric properties and manufacturing processes. The system should permit to predict the real garment behaviour acting on the parameters characterising its physical model in order to reduce the number and the role of the physical prototype.
The first one involves drawing 2D patterns by using 2D CAD systems. Modules have to be developed to generate, starting from 2D patterns, data necessary to define the 3D physical model of the garment and execute the simulation. The latter, more innovative, consists of the design of 3D garments around a digital mannequin. This technique is more natural and creative, because it allows direct transference of the garment concept.
The mode list uses 3D graphic tools, the 3D Modeler and the 3D Simulator, to both design and simulate the garment. The 2D patterns are automatically generated as well as data for assembling and positioning 2D patterns around the mannequin to define the physical model. The author followed the second approach, even if different solutions have to be adopted for men and women garments.
Virtual try-on: In the course of the project Virtual Try-On, innovative VR technologies have been developed, which form the basis for a realistic, three-dimensional, (real-time) simulation and visualisation of individual customers and garments. Utilising these VR techniques, an integrated virtual shop infrastructure is provided, which facilitates the presentation and trade of individualised garments at the point-of-sales and soon over the Internet. Instead of replacing the current shopping experience (e.g., really touching garments and materials), Virtual Try-On, in fact, aims at enhancing customer support and decision making through extending corresponding customer services.
Geometric modeling of garments: As pointed out, the standard way of designing realistic virtual simulations begins with the definition of all the necessary 2D fabric patterns, thus requiring knowledge of tailoring that is not necessarily possessed by most computer artists. The users then need to specify sewing constrains for the patterns. This tedious process is made even more complex by the need to set adequate values for a set of physical parameters and run a simulation to obtain the final shape for the garment, even then the character is at rest. The alternative is to model the garments directly in 3D, as proposed by, who developed a sketch based garment modeling tool. However, using direct modeling in 3D, the generated shape is typically not piecewise developable, and thus depicts a garment, which is not physically plausible. Moreover, the modeled garment is unlikely to depict fold patterns specific to real garments in any rest position. The author’s work enhances this alternative approach by making it usable as a starting point for modeling the static shape of realistic garment. In particular, this method approximates the garment surface mesh obtained from mask etch by a piecewise developable surface.
The developed system
3D Simulator: As already said the 3D simulator is based upon the particle-based approach. It possesses all the necessary functionality to:
References