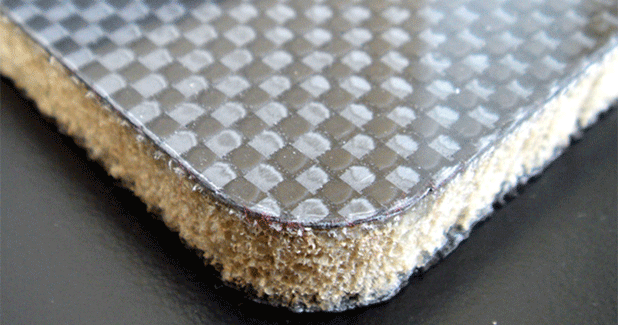
Manufacturing of glass fibre reinforced composite
Glass fibre webs are having several advantages like cost-effective process, versatility to suit the fibre and end use requirements, but these fabrics show major drawback of poor mechanical properties to suit industrial application, say Pranshil Gourkar, Aaditi Chougule and SG Kulkarni.
Glass fibre webs are having several advantages like cost-effective process, versatility to suit the fibre and end use requirements, but these fabrics show major drawback of poor mechanical properties to suit industrial application, say Pranshil Gourkar, Aaditi Chougule and SG Kulkarni.
Acomposite material is a material made from two or more constituent materials with significantly different physical or chemical properties that, when combined, produced a material with characteristics different from the individual components.
Fibreglass is a type of fibre-reinforced plastic where the reinforcement fibre is specifically glass fibre. The glass fibre may be randomly arranged, flattened into a sheet (called a chopped strand mat), or woven into a fabric. The plastic matrix may be a thermosetting plastic – most often epoxy, polyester resin – or vinyl ester, or a thermoplastic. The glass fibres are made of various types of glass depending upon the fibreglass use. These glasses all contain silica or silicate, with varying amounts of oxides of calcium, magnesium, and sometimes boron. To be used in fibreglass, glass fibres have to be made with very low levels of defects.
Fibreglass is a strong lightweight material and is used for many products. Although it is not as strong and stiff as composites based on carbon fibre, it is less brittle, and its raw materials are much cheaper. Its bulk strength and weight are also better than many metals, and it can be more readily moulded into complex shapes. Applications of fibreglass include aircraft, boats, automobiles, bath tubs and enclosures, swimming pools, hot tubs, septic tanks, water tanks, roofing, pipes, cladding, casts, surfboards, and external door skins.
Other common names for fibreglass are glass-reinforced plastic (GRP), glass-fibre reinforced plastic (GFRP)[2] or GFK (from German: Glasfaserverstärkter Kunststoff). Because glass fibre itself is sometimes referred to as “fibreglassâ€, the composite is also called “fibreglass reinforced plastic.†This article will adopt the convention that “fibreglass†refers to the complete glass fibre reinforced composite material, rather than only to the glass fibre within it.
It is often said that the textile composites are the backbone of many structural and functional advancements in modern material technologies. For textiles, the definitive definition of composites given by textile terms and definitions are as follows: A product formed by intimately combining two or more discrete physical phases, usually a solid matrix and a fibrous material. By this definition, whole fibrous composites are less usual in that they are a combination of two or more materials (fibre, web, yarn or fabric) or technologies used to gain the desired product either in terms of performance (strength, absorption, filtration efficiency, thermal insulation or to reduce the cost of the product or both. It is not necessary that a distinct interface needs to be formed; a product obtained through the combination of technologies or from blending different types of fibres may not have easily identifiable interfaces, and as constituent materials have advanced so the performance of composite structures has moved forward over the last two decades.
Ban, Bakir, Haithem [1] worked on the effect of glass fibre orientation of reinforced composite material on mechanical properties. In their study it was showed that best strength are when fibre perpendicular to tensile force then with angle 45-degree than the parallel direction and all this is less than discontinuous type strength, hardness be effected directly to number of laminated fabricated. Finally strength are increased when fibre volume fraction increase unless exceed 30 per cent of composite material.
K Devendra and T Rangaswamy [2] investigated that the mechanical properties of e-glass fibre reinforced epoxy composites filled by various filler materials. Composites filled with varying conc. Of fly ash, aluminium oxide, magnesium hydroxide and hematite powder were fabricated by standard method and the mechanical properties such as ultimate tensile strength, impact strength and hardness of the fabricated composites were studied by them. The result of experiment shows that composites filled by 10 per cent magnesium hydroxide exhibited maximum ultimate tensile strength and hardness. Fly ash filled composites exhibited maximum impact strength.
Martin Alberto Masuelli [3] explained about fibre reinforced polymers, different polymers and composites. Also preparation of different fibres which are used in composites. Basic concepts and mechanical properties of composites.
Komal Chawla and Bharti Tekwani [4] concluded that plain concrete possess very low tensile strength, limited ductility and little resistance to cracking. Fibres when added in certain percentage in the concrete improve the strain properties well as crack resistance, ductility, as flexural strength and toughness. In recent times, glass fibres have also become available which are free from corrosion problem associate with steel fibres. [5] Cem-fill anti crack, high dispersion, alkali resistance glass fibre diameter 14 micron, having an aspect ratio 857 was employed in percentages, varying from 0.33 to 1 per cent by weight in concrete and the properties of this fibre reinforced concrete like compressive strength, flexural strength, toughness, modulus of elasticity.
Asst Prof Vijay Kumar Bhanot [6] worked on composite Epoxy matrix and EP polyester reinforced material test were performed to find tensile strength, density, impact, damping of the composites for the different variables. The composites were fabricated using Epoxy resin as polymer, araldite as hardener, ep polyester as reinforcement. Single, double, and four layer composites were made and experimented in the universal testing machine and more test.
Amit Kumar Tanwer [7] concluded that glass fibre composites are considered to have potential use as a reinforcing material in epoxy polymer based composites because of their good strength, stiffness etc., in his study, mechanical properties for glass fibre composites were evaluated. Here, Glass fibre is the fibre reinforcement and epoxy polymer resin as a matrix material. Composites were prepared with longitudinal (unidirectional) and cross (bidirectional) glass fibre reinforced with epoxy based polymer. Mechanical test i.e. compression and tensile test were performed on UTM and the results are reported.
Patil Deogonda and Vijaykumar N Chalwa [8] presented work describe the development and mechanical characterization of new polymer composites consisting of glass fibre reinforcement, epoxy resin and filler materials such as TiO2 and ZnS. The newly developed composites are characterized for their mechanical properties. Experiments like tensile test, three point bending and impact test were conducted to find the significant influence of filler material on mechanical characteristics of GFRP composites. The tests result have shown that higher the filler material volume percentage greater the strength for both TiO2 and ZnS filled glass epoxy composites, ZnS filled composite show more sustaining values than TiO2.
TP Sathishkumar et al [8][9] explained about glass fibre reinforced polymer composites. Glass fibres reinforced polymer composites have been prepared by various manufacturing technology and are widely used for various applications. Initially, ancient Egyptians made containers by glass fibres drawn from heat softened glass. Continues glass fibres were first manufactured in the 1930s for high-temperature electrical application. Nowadays, it has been used in electronics, aviation and automobile application etc. Glass fibres are having excellent properties like high strength, flexibility, stiffness and resistance to chemical harm. It may be in the form of roving’s, chopped strand, yarns, fabrics and mats. Each type of glass fibres have unique properties and are used for various applications in the form of polymer composites. The mechanical, tribological, thermal, water absorption and vibrational properties of various glass fibre reinforced polymer composites were reported.
Kadir Bilisik and Gaye Yolacan [10] investigated the bending behaviour of developed multilayered multi stitched E-glass perform structures. The results indicated that the number of stitching directions and stitching steps substantially affected the bending rigidity of the developed perform structures. Stitching yarn type was also a parameter for the bending behaviour of the multi stitched. Perform structures. It was considered that the unstitched fabric structure could be easily formed whereas the directional stitched E-glass perform structure became stiff and could not be easily formed.
E Behrens [11] studied the theoretical and experimental principles of the dynamic testing of composites. He explained in detail of a steel aluminium bar, for which three independent elastic constants. For epoxy resin systems, however only the longitudinal Young’s modulus could be measured dynamically. Certain peculiarities arising from the anisotropy of the material are pointed out, and further applications and limitations of the method are discussed. Dispersion relations for longitudinal and torsional sound waves in thin bars with orthorhombic symmetry are derived by him.
Jacob M.et al [12] carried out studies in needle punched fabrics and reported that the coating and laminating can add number of features and product enhancement to nonwoven materials. This features and enhancement not only improve the functionality of nonwovens but also add value and differentiate the products. The development of nonwoven fabric has resulted from a desire to eliminate conventional textile procedures .It not only reduces the price of the fabric but also has wide applications.
Chang-Sik Ha et al [13] have studied the preparation and properties of polyurethane foamed leather and have observed that the samples show good permeability to moisture vapor by dry process. Wang et al. [14] have observed that artificial leather includes a substrate that consists of a single type of elastomeric resin provided on the substrate. This single type of elastomeric resin evenly spread on the substrate from coating. The single type of elastomeric resin is one of the components of PU, SBR& NBT etc. They observed that the density of substrate filled with particles is greater than that of coating. It was reported that, it provides undesirable laminate look to artificial leather. And these coating can easily detached or peeled from the substrate. Henri Kröling et al [15] investigated that both paper and natural fibre spun laces reinforce the resin significantly. He showed that paper can outperform both spun laces in terms of tensile strength and Young’s modulus. Even paper composites made from untreated eucalyptus pulp achieve higher tensile strengths than the spun laces. Furthermore the tensile strength of paper composites can be strongly increased by refining and fibre orientation. The fibre orientation of the paper leads to a corresponding anisotropy in the composite properties.
A significant improvement in the mechanical properties of PU resin nonwoven fabric composite was noticed by MN Satheesh Kumar et al [16]. From the water sorption results, he also observed that PU composites have higher sorption values and lower activation energy when compared with neat PUs. This may be due to the heterogeneity and the presence of voids in the composites.
The replacement of short fibres with PP nonwoven fabrics for reinforcement of cement composites especially in prefabricated concrete elements was proposed by H Pakravan et al [18] as using nonwoven fabrics increased fibre volume content in composites without side effects. Increase in flexural performance and especially the ductility of cemented composites were also observed. The comparative analysis done by Amar Patnaik et al [17] shows that with the incorporation of nonwoven fabric mat weight percentage in composites, all mechanical and physical properties of composites improve significantly. [18] These mechanical and physical properties are also improving with raise in mass per unit area of fabric mats from VS200 gsm to VS600 gsm. He also concluded that the tensile strength is better for higher fibre weight percentage for all nonwoven fabric mat composites.
In this particular project glass fibres were used to manufacture glass fibre web of three different GSMs. To this nonwoven fabrics coating of polyester resin was given in order to form the glass web reinforced composites out of them that will have some additional properties. These properties were then tested and conclusions were made.
The glass fibre web reinforced composites formed were evaluated for their performance. The results evaluated are discussed in the previous chapter, based on result and discussions:
- Tensile strength of glass fibre web reinforced composites is dependent upon both GSM as well as number of layers
- These glass fibre web reinforced composites can be drilled, so they could be used in applications where drilling is necessary
- These composites show less moisture regain as well as water absorption. So in actual usage may not be affected by presence of moisture or water
- These Composites formed can find their applications of packing, false ceiling, partitioning walls, decorative wall-piece, shipping, etc.
1.Ban, Bakir and Haithem, “Effect of Fibre Orientation for Fibre Glass Reinforced Composite Managerial on Mechanical Properties†International Journal Of Mining, Metallurgy And Mechanical Engineering, (2013), (volume 1), pp 341-345.
2.K. Devendra and T. Rangaswamy, “Strength Characterization Of E-glass Fibre Reinforced Epoxy Composites With Filler Materialsâ€, Journal of Minerals And Materials Characterization And Engineering, (2013), (volume 1), pp. 353-357.
3.Martin Alberto Masuelli, “Introduction of Fibre-Reinforced Polymers – Polymers and Composites: Concepts, Properties and Processes†Instituto de FÃsica Aplicada, CONICET.
4.Komal Chawla and Bharti Tekwani, “Studies of Glass Fibre Reinforced Concrete Composites†International journal of structural and civil engineering research.
5.Asst. Prof. Vijay Kumar Bhanot, Asst. Prof. Dharminder Singh and Asst. Prof. Puneet Sharma, “Research Work on Composites
6.Epoxy Matrix & Ep Polymer Reinforced Material†International Journal of Engineering Research & Technology. (2013), (volume2).
7.Amit Kumar Tanwer, “Mechanical Properties Testing of Uni-directional and Bi-directional Glass Fibre Reinforced Epoxy Based Composites†International Journal of Research in Advent Technology,(2014), (Vol.2).
8.Patil Deogonda, Vijaykumar N Chalwa “Mechanical Property of Glass Fibre Reinforcement Epoxy Composites†International Journal of Scientific Engineering And Research. (2013), (volume1).
9.TP Sathishkumar, S Satheeshkumar and J Naveen “Glass fibres reinforced polymer composites†Journal of Reinforced Plastics & Composites. (2014), (volume33), pp-1258-1275.
10.Kadir Bilisik and Gaye Yolacan “Experimental Determination Of Bending Behaviour Of Multi Layered And Multidirectionally Stitched E-Glass Fabric Structures For Composites†Textile Research Journal. (2012), pp- 1038- 1049.
11.E. Behrens “Dynamic Testing Of Composite Materials†Textile Research Journal. (1968), (volume 38), pp- 1075-1085.
12.Mary J. (ed.), “Needle Punched Fabrics: and overviewâ€, New Cloth Market, vol. 8, Jan-June 1994, P 13-20.
13.Chang S.H. (ed.), “Preparation and Properties of Polyurethane Leather having good permeability to moisture vapourâ€, polymer (Korea), vol.17, Sept. 1993, P 504-512.
14.Wang C, “Artificial Leatherâ€, U.S.Pat.No. US 2005/2005/0244654A1, Nov. 2005, P 1-3.
15.Henri Kröling, “Non-Woven and Paper Based Epoxy Compositesâ€, Science & Technology, June 2014, P 2-5.
16.MN Satheesh Kumar, “Castor Oil-Based Polyurethane–Polyester Nonwoven Fabric Composites: Mechanical Properties, Chemical Resistance, and Water Sorption Behaviorat Different Temperaturesâ€, Journal of Applied Polymer Science, vol 105, issue 6, 2007, pp. 3153-3161
17.H Pakravan, “Application of polypropylene nonwoven fabrics for cement composites reinforcementâ€, Asian journal of civil engineering (building and housing) vol. 12, no. 5 (2011), pp 551-562
18.Amar Patnaik and Sachin Tejyan, “Mechanical and visco-elastic analysis of viscose fibre based needle punched nonwovens fabric mat reinforced polymer composites: part 1†Journal of Industrial Textile, pp 1-18.
19.Slayter patent for glass wool. Application 1933, granted 1938.
20.a b c Loewenstein, K.L. (1973). The Manufacturing Technology of Continuous Glass Fibres. New York: Elsevier Scientific. pp. 2–94. ISBN 0-444-41109-7. The authors of this article are from DKTE’s Textile and Engineering Institute, Rajwada, Ichalkaranji, Maharashtra 416115.