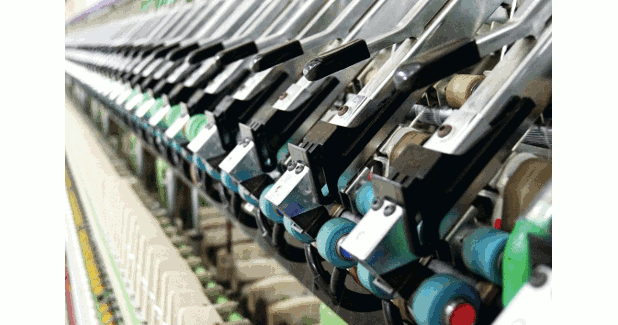
Lakshmi suction compact spinning system
Lakshmi suction compact system fulfills all technological requirements to produce good compact yarn. History stands as a documented proof of LMW’s success.
Lakshmi suction compact system fulfills all technological requirements to produce good compact yarn.
History stands as a documented proof of LMW’s success reflecting phenomenal growth through technologically-advanced products. LMW has proven this over five decades through its products and has now once again demonstrated with its technologically-advanced Lakshmi suction compact system. LMW, standing by its commitment of providing world-class technology and cost-effective solutions, has enriched the features and the stable performance of its suction compact system by identifying the varied needs of customers and ever-changing quality demands.
Features
- Suction nozzle to work with single yarns and SIRO yarns Quadra suction nozzle with top suction – to enhance user friendliness
- Direct loading system for top rollers – for uniform and consistent yarn quality
- Perforated rubber apron – for better compacting and less cleaning requirement
- Special spinning angle for enhanced machine performance
- Lesser power consumption
Suction compact system arrangement
Better compacting begins with better drafting of roving. The fourth bottom roller is driven by servo motor to deliver the compacted yarn with utmost accuracy. This separate drive for the fourth roller ensures that there is no additional load on the drafting drive. The roving from bobbin passes through main drafting zone of 3 over 3 pneumatic drafting system, gets drafted and material is guided over the perforated apron. The apron is placed on the nozzle assembly containing a suction slot. Tension draft could be easily adjusted with a single touch in the screen.
Lakshmi suction compact system fulfills all technological requirements to produce good compact yarn:
- Well-designed suction slot and suction nozzle
- Better guiding of the compacted fibre strand to the nip of delivery roller
- Uniform suction throughout the machine
- Perfect fibre guidance through perforated aprons
- Fluff accumulation-free compacting zone
- Easily adjustable tension draft mechanism for technological fine tuning
Direct loading system (DLS)
DLS for the guiding roller ensures optimum load to deliver the best quality yarn. With DLS, the quality of the output yarn can be optimised and load on the roller can be easily adjusted. Top arm load can be maintained like a regular machine and the distance between the compact delivery roller and front top roller can be precisely adjusted to enhance the performance.
Suction arrangement
Top suction nozzle unit, with its unmatched ease of operation, ensures effective suction system for compacting. A single suction nozzle tube ensures suction for four spindles, thereby easing the work for operators during cleaning and maintenance. Varying boot diameter across the length of the machine ensures uniform suction, thus ensuring that every spindle produces better quality yarn with uniform compacting.
Special spinning angle
LMW always fulfills its responsibility of integrating the inbuilt machine design advantages to ensure that its customer enjoys the benefits to its fullest. Keeping this in mind, LMW has implemented a special spinning angle for Lakshmi compact spinning system, which makes the yarn stretch length lesser, yarn tension lower, better twist flow up to the nip and finally gives the comfort of reduction in end breaks up to 20 per cent.
The versatility of Lakshmi suction compact system to work with cotton, polyester, regenerated polyester, viscose, modal, micro modal, PV blends, PC blends, melange, bamboo, modal cotton blends, tencel and for the applications of weaving and knitting has made the system to get accepted by top end spinners, and hence LMW could increase its compact spindle base to 1.5 million spindles within a short period.
Power consumption
Innovation from LMW always strives towards reducing energy consumption for the production process and thereby making the production cost of compact yarn always lower. This is made possible by well-augmented suction ducting system and nozzle design. Nozzle has been designed in such a way to meet the suction requirements of each spindle with minimum suction loss and thus conserving precious energy.
Advantages of Lakshmi suction compact system include:
- Perfect compact yarn
- Increase in yarn tenacity by up to 15 per cent
- ZWEIGLE yarn hairiness S3 reduced up to 85 per cent
- USTER – hairiness index improvement up to 30 per cent
- Yarn imperfections and classimat faults – Improvement achieved
- Process advantages – ring spinning and downstream process
- Lesser TM to get same yarn strength and increase in productivity up to 10-15 per cent
- Enhanced ring spinning machine performance and lesser end breaks
- Reduced ends down during warping
- Increased efficiency of looms
- Less singeing
- Reduced spirality of knitted cloth and hence better dimensional stability
- Better raw material management
- Cheaper raw material can be used to get same yarn quality
- Possibility to reduce/optimise comber noil %
The consistent efforts made to meet the stringent quality requirements of downstream processes and ever-changing market demands has transformed Lakshmi suction compact spinning system to achieve high standards of results. Adding to the above, the advantages in Lakshmi suction compact system are lesser investment cost, lesser power and maintenance cost, quick return on investment and close networked after-sales service support.