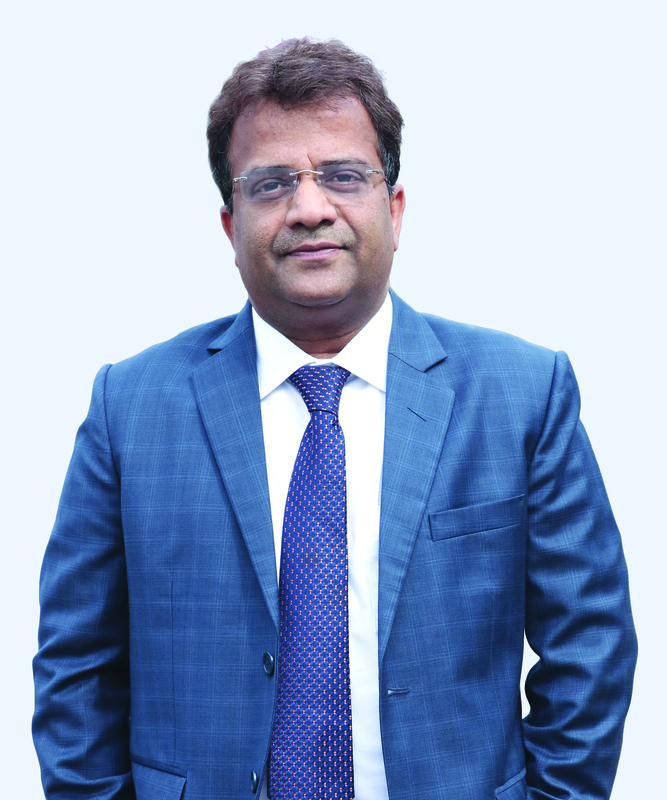
Making traceable products should be the goal in textile value chain
Stovec Industries incorporated in 1973, is a subsidiary of SPGPrints B.V., The Netherlands. Stovec, as a holistic printing solutions provider, offers a product portfolio that includes capital & consumables range of products for textile printing industry.. In this conversation, Shailesh Wani, Managing Director, Stovec Industries, shares the development of textile printing over the years and the benefits of digital printing with Divya Shetty.
How has printing on textiles changed over time?
During the last few decades, there have been rapid advancements in textile printing technology, particularly in terms of the machinery used for printing, print manufacturing and post-treatment of printed fabrics, in order to meet the demand for high rates of production and complexity in printing. Major trends like population growth, increasing purchasing capability and rapidly changing fashion trends have been the key drivers for growth in the textile printing market ever since.
If we see our SPGPrints history, we entered textile printing market in 1958 with a flatbed machine, followed by the revolutionary invention of rotary screen printing in 1963. As time progressed, we developed into an internationally acknowledged authority in rotary textile printing, dedicated to bringing colour to the world. Very earlier, we realised that next to the rotary screen printing technology, digital textile printing shall be on the rise. So, in 1991 we were the first in the industry to launch a digital textile printer and are now a key international player in global market for digital textile printing. Today, the consumers are becoming more demanding and looking for creative and unique designs, also sustainable solutions at the same time, thereby leading to shorter printing runs. So embracing digital printing today is the driving force for fashion as well as home décor industry in future. Moreover, this method of textile printing today is more easier, environmentally friendly, and cost-effective.
What steps has the Indian textile industry taken to adapt to new-age printing?
The companies have started to take keen interest in technological innovation and are investing in its development and application in the garment and textile industry. Many home textile companies in India are also leveraging strategic partnerships to strengthen their business operations and foothold in the country. They are using technology to optimise the value chain.
Also, today the consumers have become more conscious of the environment and are interested in products that augment sustainability. So, market players have dedicated themselves to create eco-friendly technologies/products and look forward to maintaining collaborations to focus on sustainability. SPGPrints takes pride in providing the Indian Industry with sustainable printing solutions.
With a rotational shift happening in the industry, it has become essential for the companies or brands to stay ahead of the latest trends and styles while also managing costs and maintaining profitability.
Kindly elaborate on the benefits of digital printing.
Digital textile printing is the fastest growing segment within textile printing industry. More & more printers are making the transition or expansion from rotary to digital textile printing, as it is able to meet today’s demands for short-runs, fast-turnarounds & sustainability. By using digital technologies, higher standards of quality on the widest range of fabrics can be achieved, maximising uptime, and giving customers the flexibility to bring many creative ideas quickly to the market. The digital printing technology has broken some major boundaries that rotary printing used to put on designers & production people earlier.
SPGPrints have regularly been posting blogs on website for our customers to get detailed insights on topics for both digital & rotary textile printing technologies, their advantages and opportunities in future.
What is the latest innovation done by the company in printing?
SPGPrints has committed ourselves for introducing the latest innovations in both rotary and digital textile printing for the fashion and the home-furnishing industry.
In digital textile segment, we launched the new robust entry level digital printer – DART for our Indian customers who want to kick start their journey in digital textile printing. We also introduced the addition of 3 new digital printers in the portfolio – Rose, Jasmine, and Magnolia, that focused on maximum productivity at optimal print resolution. Rose is a roll-to-roll paper sublimation system with a maximum resolution of 1200dpi, the print quality offered is excellent. Jasmine and Magnolia are direct to fabric systems that will enable our customers to extend their offering in digital printing. Jasmine focuses on maximum productivity at the most optimal print resolution where Magnolia with its true 1200 dpi and Archer+ technology raises the bar to new levels of print quality.’
In rotary, we recently launched in India ITME’22 our latest innovation in rotary portfolio – Teak, a 2.45 meters wide rotary printing machine with Universal Repeat functionality. Teak is the latest generation of the Pegasus series that has opened a wide-spectrum of applications for our customers worldwide, allowing them to print on woven and knitted fabrics for fashion and home textiles. All repeat sizes from 640 to 1018 mm can be printed in the same machine without any modification of parts. What is also unique to the Teak is that both squeegee types can be combined in a single position. This gives the utmost printing flexibility, and is ideal for optimising effects such as half tones, fine lines and blotches.
How is the government helping the printing industry in India?
I believe Indian textile & clothing industry was one of the few industries to quickly bounce back post pandemic, thanks to few government initiatives in it. The China+1 policy of global buyers had put India strongly on global textile map as an dependable destination, however, the recent performance in global trade wasn’t promising enough due to high cost of production. Industry saw great instability in parameters during the pandemic, post-pandemic and Russia-Ukraine War, such as demand, consumption, transportation, consumer behaviour, supply chain management, export and import, and production.
However, to overcome these after-effects on textile printing industry, the government is now stressing on an economic vision, based on increasing production, export and generating employment, and various policy initiatives including “Skill India” and “Make in India”. Under the PM MITRA scheme, 7 Seven Pradhan Mantri Mega Integrated Textile Region and Apparel Parks shall be set up by 2027-28 to attract investments in country and generate many new employment opportunities. Additionally, the government is implementing various schemes under the A-TUFS, SITPs, SAMARTH & many others exclusively for promotion and development of textile sector on pan-India basis.
Apart from these, the core support required for industry survival is in getting raw material of required quantum of quality at nominal cost, which is yet to become reality in near future.
What challenges does a printing company face in India and globally? Do you have any advice for other users?
The biggest challenge faced by our industry is competitiveness at global level. The Indian textile sector confronts competition from neighbouring countries like Bangladesh, Indonesia, and Vietnam who have increased their export share by taking advantage of Free Trade agreements. The imports have risen sharply due to their low-cost clothing and safety regulations.
Also, I feel our industry do not lack the ability or the subject expertise, but we definitely lack scale. Availability of good quality raw material (like cotton, nickel etc) is the setback.
Also the infrastructure bottlenecks, i.e having very obsolete machinery and slow acceptance of modernisation and technological innovations have lagged us behind markets of China & Europe. The clustered development of sector, lack of automation in industry, & cost of certification of stringent social and environmental norms are few other factors that affect the printing industry.
Do you have any advice for other users?
By anticipating the future market trend, there is a need for companies to capitalise by investing into different printing products or technologies. To keep up pace with the requirements of buyers in export markets and responsiveness, the exporters can have better competitiveness.
Also making traceable and sustainable products should be the goal in textile value chain process in near future, if companies are targeting to exports apparels to western markets such as the UK, the EU, and the US.
What is Stovec Industries planning to present at ITMA 2023?
At ITMA 2023, SPGPrints will help you with optimising your digital and rotary printing workflows and showcase the latest innovations in textile printing for the fashion and the home-furnishing industry. For printing companies who are ready to embark on a digital textile printing journey, a visit to ITMA Milan 2023 will definitely be worthwhile, as you will witness the latest addition of digital printers in our portfolio. Also, SPGPrints shall showcase its latest innovation in rotary textile printing segment – TEAK, a wider width rotary printing machine with universal repeat functionality, along with various rotary screens to solve our customer’s daily printing challenges.