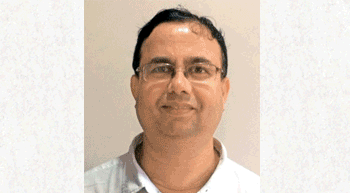
The changing face of textile printing
With the advent of inkjet printers and wide applications of inkjet printing in various areas, printing on fabrics also developed. It is a change from conventional method of screen printing - flat bed and roto. Digital printing offers distinct benefits of being able to print attractive design, complex designs, printing in short runs (smaller batch size), easy sampling, and capability of printing anything that you see on a computer screen. It has infused new energy into printing ideas and garment fashion. In a way, it is revolutionary!
– Shashank Ruiwale, Managing Director, Indigo Prints Smart Private Limited
With the advent of inkjet printers and wide applications of inkjet printing in various areas, printing on fabrics also developed. It is a change from conventional method of screen printing – flat bed and roto. Digital printing offers distinct benefits of being able to print attractive design, complex designs, printing in short runs (smaller batch size), easy sampling, and capability of printing anything that you see on a computer screen. It has infused new energy into printing ideas and garment fashion. In a way, it is revolutionary!
Process of digital printing for various fabrics [polyester, cotton, silk, jute, etc.] are different with all ingredients also being different. The article focuses on polyester fabrics and its blends.
Process of printing on polyester fabrics can be broadly of two types – transfer printing and direct-to-fabric printing. Transfer printing is the most popular method, being widely in use today. Transfer printing requires large format inkjet printers with capability to print with dye sublimation inks, sublimation paper rolls and heat transfer press. Design is prepared in the computer with the help of software like CorelDRAW, Adobe Photoshop, etc. and printed using larger format inkjet printers. These printers use dye sublimation inks and paper coated with sublimation, which is a process of converting liquid to gas. Polyester material reacts with sublimation inks and sublimation coating chemical under heat and pressure and image is transferred. Image quality is good, water fast, wash fast and qualifies for high standards in the textile industry.
In 2012, it was mainly Mimaki, Roland and Mutoh who built printers using Epson Piezzo printheads suitable for sublimation inks. Later in 2014, Epson also added to the range with F series dye sublimation printers and many Chinese manufacturers also started developing printers around Epson printheads. As Epson started controlling supply of printheads, other manufacturers like Konica Minolta, Ricoh, Fuji Dimatix, Panasonic, Kyocera also started to offer Piezzo printheads suitable for this industry. These new generation of printheads were more durable, built for heavy duty industrial use and also faster in printing speeds. However today, Konica Minolta and Ricoh are widely successful in offering wider range of printheads at affordable prices.
A large format printer of 24 to 72 inch printing width and printing speeds of 8 sq m per hour to 50 sq m per hour is the wide range of product specifications.
In order to select proper printer suitable for your requirement, one must plan for production in sq m in a day. For example, entry-level Epson F series printer offers 14 sq m (4 pass) and 22 sq m (3 pass) per hour.
While entry-level Roland, Mutoh and Mimaki printers offer 12 sq m per hour. Chinese printers based on DX5/DX7 printheads offer 12 to 16 sq m per hour in 4 pass quality. For more production, one can select printer with two printheads, which normally will deliver double output. For larger production of 1,000 sq m per day (20 hours printing), one needs to select printer with four printheads or two printers with two printheads.
Ink quality is important in order to get steady production, consistent quality, trouble-free performance and long printhead life. Ink is also important to get good fluorescent colours and print quality. Quality of sublimation ink along with RIP software decides the print output quality and ink consumption. Normally 3 ml to 6 ml per sq m is the consumption of ink for transfer printing. Though there are many factors that has influence on this parameter – like number of head cleaning cycles required, colour coverage in design, image density (darkness), etc. It is essential to have ink quality which needs least number of head cleaning cycles. This can be one broad parameter which indicates ink quality.
Sublimation paper is also important for the quality of printed designs. These are coated papers that do not absorb ink, keeps it on the surface and is able to transfer 90 to 98 per cent of the ink to fabrics. However if paper is non-absorbing type, it also has high drying time, which is deterrent for productivity. Thus your printer needs dryer and heater which can dry printed image quickly. These are mostly provided by all Chinese printer suppliers, while branded suppliers charge heavily for these accessories.
Heat press machines are mainly two types – flat press and rotary press. Combination is both is also available. Flat press is suitable for ready-made garment manufacturers who are producers of children wear, ladies tops, kurtis, lehengas, t-shirts, etc. While roller press is used for fabric length manufacturing like saris, dress materials, furnishing fabrics, etc. Normally heat press machines of 30 x 40 inch (or 36 x 48 inch) and above, with double tray for improved productivity, is the most popular choice. Double tray offers more production per hour, lesser electricity consumption and lower labour cost. While 72-inch wide roller press is a preferred option for fabric length printing.
This method of transfer printing on polyester fabrics is suitable for various blends like chiffon, georgette, viscose, satin, etc., however make sure that fabric has at least 50 per cent polyester content. Print quality heavily depends on polyester content in the fabric.
Today, there are many options available in this which are similar in appearance and feels like cotton, but is synthetic material.
Direct-to-fabric printing for polyester is not very popular, mainly because it requires expensive printers if the fabric is of stretch type. And about 90 per cent of garment polyester is stretch type. Print output quality is also marginally inferior as compared to transfer printing; however nowadays few inks are available that offer far more improved print quality in direct printing. These are called disperse inks or disperse sublimation inks.
We are at the threshold where sublimation transfer printing is evolving and improving in order to offer higher productivity at lower costs and more durable technology offerings. However digital printing brings in ‘n’ number of advantages like overall lower cost of garment printing, specially in short runs and quick delivery like you can offer garments in 6 to 10 days after approval of samples. Repeat printing orders are very easy to process as you just need to refer to your design in a computer, no more physical storage of screens. Process is highly eco-friendly with no liquid effluents. Although the matter of concern could be the gaseous effluents, which are been released.
This story is the first part of a 3-part series.