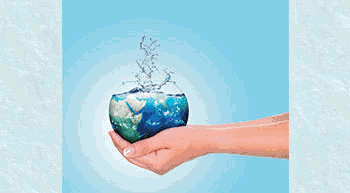
Is India ZED-Ready
If the textile industry in India does not achieve zero effluent discharge (ZED) in the next few years, it will not only affect the socio-economic environment but also even export to countries where “green label†is now becoming mandatory, reveal Joseph S and Karthik M. Zero effluent discharge (ZED): It is a drive that has been happening only in fits and starts in India. When the present Indian government initiated a draft regulation only a few months ago, which will make ZLD (zero liquid discharge) mandatory for textile units having waste water discharge of more than 25 KLD (kiloliters per day), the pollution issue surfaced again.
If the textile industry in India does not achieve zero effluent discharge (ZED) in the next few years, it will not only affect the socio-economic environment but also even export to countries where “green label†is now becoming mandatory, reveal Joseph S and Karthik M.
Zero effluent discharge (ZED): It is a drive that has been happening only in fits and starts in India. When the present Indian government initiated a draft regulation only a few months ago, which will make ZLD (zero liquid discharge) mandatory for textile units having waste water discharge of more than 25 KLD (kiloliters per day), the pollution issue surfaced again. Textile dyeing contributes 20 per cent to industrial pollution and sordid stories of closure of many units in Tirupur (Tamil Nadu) following High Court order a few years ago and the very recent closure orders in some Rajasthan units were eye-openers. But are we ZED-ready is a million-dollar question!
It is also well-known that a few surveys have brought out the fact that some of the central effluent treatment plants (CETPs) and effluent treatment plants (ETPs) implemented have been neglected, and setting up such plants is only an eye-wash. Despite the problems dogging the textile industry regarding pollution due to effluents discharge, the industry is veering round to the view that ultimately saving water from pollution is saving humanity from destruction. To save costs and reduce the capacity needed, comprehensive water audits are usually performed which also ensure that the system deals only with the most polluting streams. Installing ZLD technology is therefore often beneficial for the plant’s water management; encouraging close monitoring of water usage, avoiding wastage and promotes recycling by conventional and far less expensive solutions.
Avinash Mayekar of Suvin Advisors describes: “ZLD means zero or no discharge of wastewater or any liquid effluent from a factory to outside surroundings. The entire wastewater generated due to processes inside a factory has to be treated and recycled back into the factory! ZLD – it is not a single system but a combination of various treatment processes which may vary from industry to industry. This is due to the fact that the type to technology depends upon the quality of effluent and process water quality requirement.â€
He suggests, “In order to achieve ZLD, we have to recover the water and salt separately from the effluent and reuse it in the dyeing process. As a simple explanation, the effluent is treated in an ETP comprising primary, secondary and tertiary treatment steps. The treated water is recovered from the membrane processes such as ultra filtration (UF), nano filtration (NF) and reverse osmosis (RO) during tertiary treatment phase and salt is then recovered by using multiple effect evaporation (MEE) with crystallisation.â€
“ZLD technology and experience is only about 10 years old and has made rapid improvements during this decade. What was once thought as impossible has been successfully demonstrated. Of course lack of experience and technology worldwide created several challenges in implementation of this project resulting in closure in 2011-12, however with the development of ‘treated brine reuse technology’ by the Tamilnadu Water Investment Company Limited (TWIC) and the support of Tamil Nadu Government, CETPs have now been successfully in operation for the last four years,†says I. Sajid Hussain, Head O&M (Water Reuse), TWIC.
Tirupur: Leading from the front
Tirupur was the first industrial cluster to implement ZLD in the country and the first in the textile cluster in the world. The Tamilnadu Water Investment Company Limited (TWIC) was promoted in 2000 by the Government of Tamil Nadu and IL&FS, essentially as an investment vehicle to implement 185 million litres per day (MLD), Rs 1,000 crore, New Tirupur Area Development Corporation Limited (NTADCL) water supply project in Tirupur for supply of water to the industry and the municipality.
Based on court directions, the industry wanted to implement ZLD. TWIC developed nine CETPs and is currently operating seven of them in Tirupur. The combined capacity of the nine CETPs is about 53 MLD. Says Hussain, “As per directions of Chief Minister of Tamil Nadu, TWIC is now carrying out diagnostic study and detailed project reports (DPRs) for over 12 clusters in Erode, Nammakkal, Salem and Karur. This will cater to over 2,000 dyeing units in Tamil Nadu. The Government has earmarked Rs 700 crore for these projects. Two projects namely Kariyapatti CETP in Virudhunagar and Kadayampatti CETP in Bhavani have been accorded in-principal sanction for 50 per cent funding under IPDS scheme by the Government.â€
The Tirupur project developed by TWIC has won several recognition including for the Highly Commended Industrial Water Project of the Year 2014 from Global Water Intelligence, UK; Industrial Water Reuse Project of the Year 2014 from WateReuse Association USA and Corporate Water Stewardship Award 2015 from GWI, UK showing the global recognition and actual success of the project.
Other companies following suit
Thane-based LANXESS offers a whole range of innovative products that helps to tap, safeguard, and inexpensively purify water – and to effectively reduce the waste of water. LANXESS offers a whole range of innovative products that are used in the textile industry, the applications of which extend from textile auxiliaries, fibres, softener, lamination, and dyestuff.
Speaking about the strength of Lanxess in terms of tech supplier to the textile industry, Prakash Shanmugam, GM, Head of BU-Liquid Purification Technologies at LANXESS India Pvt Ltd, avers, “Our main focus is on two kinds of products – One is the ion exchange product line and the other is the reverse osmosis (RO) line.â€
“The customers are well aware of the country’s situation. One thing is awareness but the next things is to get educated on what one should do. Our main mission is to educate the industry, and that is why last year we organised the big seminar which received a good response. Industry people from areas like Erode attended the seminar and since we have the technologies and solution, they were keen to put them into action. Of course, it is going to be costly, but somehow we have to do it. Because environment protection is of primary importance today in a world, which is getting polluted day by day. The Government on its part should also be stringent and use all conditions and orders to curb pollution,†he further adds.
Even Mumbai-based Enviro Analysts & Engineers Pvt Ltd is not far behind. Rohan Desai, Director of Enviro Analysts & Engineers Pvt Ltd, says, “We have done many projects for the textile industry. We have worked for Welspun, Detco Textiles, and have provided consultancy to SK Garments and many more. There are at least 7-8 projects in Tarapur itself. We have done their turnkey projects, we have found solutions for their issues with the solutions control board and made sure that solutions control board has no issues with this.â€
Ion Exchange has been promoting the use of efficient technologies that can treat wastewater effectively and also recover water as well as salt/valuable by-products in some cases to improve the economic viability of such projects. The company provides innovative treatment schemes incorporating state-of-the-art biological treatment systems in combination with membrane systems to tackle the two major problems facing the textile industry concerning waste water management:
JP Pathare, Sr VP of International Division, Ion Exchange (India), revealed, “The demand for water and wastewater treatment solutions has increased. Customers are more open to embrace new technologies, although they are a bit expensive, but this is confined to mainly large and medium scale companies who have invested in setting up captive effluent treatment plants.†He further added, “Now, companies are setting up goals for sustainable development through a cleaner environment, reducing pollution, producing less waste by adopting advanced technologies and conserving the environment. Many MNCs and major Indian groups have set up internal goals. This is the reason many companies are adopting recycling technologies.â€
“Those who are environmentally-conscious are opting for ZLD technology, though it is a bit expensive as zero waste means that waste at the end has to be evaporated thermally or by solar. We have commissioned five major projects so far; one outside India and the rest in India, and a couple more are currently under execution,†said Pathare.
ZLD: A reality!
Hussain of TWIC concludes, “Implementation of ZLD will also push the boundaries for technology, which today still comes from the developed world. Countries like Bangladesh too are considering implementing of ZLD by 2021 for their textile sector and are learning from the Indian experience. Countries like China too have started implementing some ZLD projects in the coal to chemicals sector. As compared to most developing countries, we have formulated stringent laws, implemented CETPs all over the country, however we lack in their successful operation due to lack of incentives.â€
“Majority of textile units are planning for ZLDâ€
M umbai-based A.T.E. Enterprises Pvt Ltd is a multifaceted engineering group offering world-class products and solutions spanning several segments. Under wastewater treatment, A.T.E. Enterprises provides comprehensive range of wastewater treatment and recycling solutions for various industries.
S Rajendran, VP (Textile Engineering, Processing, ETP & Utilities), A.T.E. Enterprises, in an interaction with the ITJ team.
How important are ZED and other ZLD’s are for the Indian industry at this juncture? With the growing scarcity of water, every dye house/processing needs to be self-sufficient by generating its own water. Also, it should be our social endeavour towards society not to damage the environment any further.
What are the current thinking & scenario globally in textile industry in this matter?
In the global market, effluent treatment is being considered as a serious matter and many of the countries follow the norms strictly. Across India, the awareness has been created and the Government is very strict on the norms. The processing units are focusing on the matter with lots of seriousness and they are committed. Majority of the units are planning for ZLD.
What are A.T.E’s offers in ETP and CETP for the Indian textile industry?
A.T.E. has its unique AAA Technology, which has gained good acceptance in the recent past. Reduction of colour, COD, BOD and other pollutants without the use of chemicals have been successfully achieved through our technology.
A.T.E can offer a complete package solution like ETP, RO and ZLD. Our scheme is based on biological treatment by which we can reduce the consumption of chemicals which will also result for lesser sludge formation. We do have a strong service team which will ensure smooth execution and we do give necessary training at site
Can you briefly give us a case study of ETP application in the domestic industry?
Jeyavishnu Tex Processors, Tirupur is a classic example of 100 per cent ZLD. Their team along with ours took up the challenge and today they are achieving almost 95 per cent recovery of water and 100 per cent Glouber’s salt recovery in their plant. The entire plant was supplied by us and the customer is very happy with the performance/scheme.
Can you share with us some ballpoint figures on how much penetration has ZLD made in our country?
States like Tamil Nadu, Andhra Pradesh, Karnataka, Gujarat, Madhya Pradesh are now totally ZLD states. You cannot set up a process house in these states without the PCB’s consent to operate. Other states like Punjab, Delhi NCR are following suit. Almost all the existing process houses are planning for at least RO for reusing the water.
What should the Government and industry do to take mission ZLD on a larger scale?
Subsidies, special sanctions under TUF’s, very low interest rates are some steps the government should take to promote ZLD. In turn, the industry should reciprocate by installing the best/sustainable technology so as to make the ZLD concept a success. Awareness should be created for students by teaching them the environment science in the college.