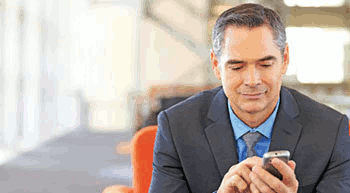
SPIDERweb: The way to an economic spinning mill
SPIDERweb, the basis module, is today the well-known and proven SPIDERweb system, writes Marcel Rengel. SPIDERweb of the latest generation is the only mill management system that collects, displays and analyses all relevant data from the spinning preparation to all four spinning systems as well as providing support.
SPIDERweb, the basis module, is today the well-known and proven SPIDERweb system, writes Marcel Rengel.
SPIDERweb of the latest generation is the only mill management system that collects, displays and analyses all relevant data from the spinning preparation to all four spinning systems as well as providing support. Rapid identification of production deviations and timely intervention increase the production and thus the economic efficiency of the spinning mill. Permanent monitoring reduces routine tests and ensures consistent quality.
Monitoring systems began their move into the spinning mill with the collection of data and monitoring of the machines and operating processes. The next development stage is that the control systems of the future can provide help in finding solutions to problems. With this integrated advice, industry 4.0 will find its way into the Rieter spinning mills.
SPIDERweb
The modular design of SPIDERweb enables any number of machines to be connected (Fig. 1). Future modules can be easily integrated at any time.
SPIDERweb, the basis module, is today the well-known and proven SPIDERweb system. It forms the foundation for connecting further hardware and software modules. SPIDERweb has been continually modernised and further developed for more than 20 years. Over 10 000 machines in nearly 50 countries globally are already connected. Tried and tested modules such as the WallBoard and the individual spindle monitoring ISM are integral parts of the system. The SPIDERweb world has been and will be supplemented by new, useful modules.
Alert and Cockpit Modules
The plant manager defines which parameter transgressions he wants to be reported to him. Should a value be exceeded or not reached, a short notification will be sent to his smartphone. He therefore has complete control of his spinning mill and must make far fewer tours of inspection. This gives him time for other important duties.
The quality manager sets the alarms as he considers appropriate. Reject quotas can be reduced due to quicker response times. The yarn buyer enjoys the high yarn quality consistency of his supplier.
Quick monitoring after receipt of an alarm or a faster overview at the end of a shift – the Cockpit Module provides a view of the most important spinning mill data from every location.
Climate Module
That climatic conditions in a spinning mill exert a textile-technological influence on the running behaviour and the quality is a well-known fact.
With the help of the temperature and humidity sensors, current values are constantly shown on the WallBoards and are simultaneously transmitted to SPIDERweb. Efficiency reductions without any discernable reason gain transparency. Frequent start-up spinning reruns by robots, e.g. on the rotor spinning machine, become explainable.
Assistant Module
SLIVERprofessional allows easy problem management of periodical faults on Rieter draw frames. The fault search is simplified and accelerated. Indication regarding the cause of the fault is visually displayed. Long fault diagnostics are therefore a thing of the past. Setting recommendations for each material and sliver count help right from the start to take the right path.
Rieter Spinners’ Guide
Is a search being made for a new textile application or should the product range be expanded? Is experience for the implementation lacking? The integrated Spinners’ Guide helps and guides directly along the right path.
In addition to process recommendations from the bale processing to yarn manufacture, detailed spinning recipes for all spinning technologies are readable, based on the textile application. Filter functions help to find the right recipe according to application, material or yarn count.
The Guide shows which components are needed and how they are used. The way to an optimal, new textile product thereby leads more quickly to success.
Sustainable yarn production
The energy consumption in the spinning mill is not only a decisive cost factor, but also is important for sustainable yarn production. Verification of the energy consumption is increasingly required – from authorities or for reporting to customers. The Energy Module helps to record the energy consumption per kilogram of yarn, simplified and reproducible.
The author is Technical Head, SPIDERweb Data Systems, Rieter. He can be contacted at: marcel.rengel@rieter.com