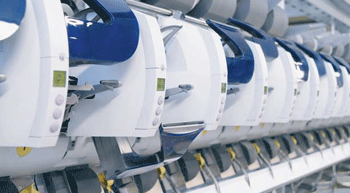
New dimension to rotor
The single-drive technology of the Autocoro 8 is catapulting the automation of the rotor spinning mill into a new dimension. This intelligent technology relieves spinning mills of the burden of organizational tasks.
The intelligent automation of the Autocoro 8 will change the production processes in a company.
The single-drive technology of the Autocoro 8 is catapulting the automation of the rotor spinning mill into a new dimension. This intelligent technology relieves spinning mills of the burden of organizational tasks. Machines with smart, autonomous spinning positions can be integrated far more easily into operating processes than conventional rotor spinning machines. Automatic processes that are stiff and inflexible on belt-driven machines suddenly become adaptable and can be optimized better, enabling companies to attain their goal of maximum efficiency with much less effort.
Smart spinning positions start up faster
Every spinning position on the Autocoro 8 is an intelligently automated, independent production unit with individually controlled spinning and winding processes. The intelligence is there where it is needed: at the spinning position. All Autocoro 8 spinning positions can piece independently. They don´t need to wait for a central unit, as on belt-driven machines. The Autocoro thus comprises 552 intelligent production units, which are productive round the clock without exception, even when piecing is required especially frequently at some spinning positions. On start-up the individual automation of the Autocoro also results in an unassailable leap in productivity. The QuickStarter facilitates twelve synchronous piecing processes, meaning that the Autocoro 8 runs up 6 times faster than a comparable machine with a belt drive.
Smart spinning positions show what they´re doing
Autocoro´s smart spinning positions communicate with the operating staff. A symbol display at each spinning position shows what the position is doing at any moment. If a malfunction occurs, the display signals what the problem is, so that the operator can quickly rectify the fault without any tedious troubleshooting process. Machines with a central drive have coloured LED signals at the spinning position at best, or fault messages on the central operating screen at the end of the machine. This delays fault elimination and extends the production stoppage.
Flowing lot change in ongoing operation
The Autocoro 8 is the first rotor spinning machine that achieves a flowing lot change entirely automatically. As soon as a spinning position has completed the last package of the first lot, it automatically begins with the next lot – with no manual intervention required.
The individual spinning position supports reliable lot separation even when changing cans or spinning components; there is no need to wait for all spinning positions to run out, as on conventional belt-driven machines. Once the last package in the old lot is full, the spinning position automatically adopts a waiting position, indicated by a light signal. The operator can now change the spinning can or component and acknowledge the new batch on the spinning position. Long stoppages and spikes in the workload during lot changing, such as are common on machines with belt drives, no longer occur.
The automatic, intelligent lot separation opens up new possibilities for economical, quality-oriented raw material utilisation in spinning mills, as configuration of the individual spinning position can be adapted automatically according to batch. This makes it possible to achieve a constant yarn quality for each lot at full production capacity with varying raw material quality.
The spinning position knows when the rotor needs to be cleaned
Decentralised automation of the individual spinning positions also prevents pointless work spikes in cleaning processes. The Corolab sensor monitors the yarn quality at each spinning position continuously and so it recognizes whet