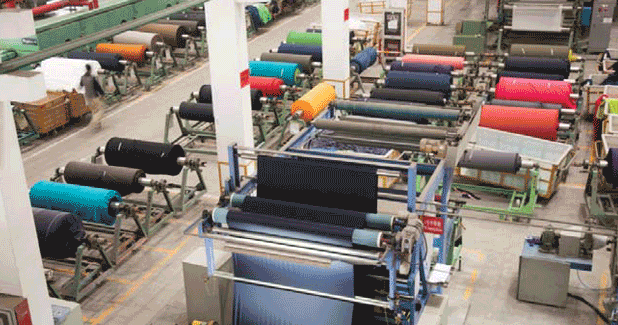
Modernisation for textile industry: Today & tomorrow
It must be ensured that the better technology levels that are adapted must give higher production levels at the same operating cost achieved earlier, says Avinash Mayekar.
It must be ensured that the better technology levels that are adapted must give higher production levels at the same operating cost achieved earlier, says Avinash Mayekar.
The global textile scenario is at a stagnant stage. A revolutionary demand as in case of smart phones is not the trend that is experienced in textiles. Anticipations have just not worked out the way it should have happened for many years. There is an usual scenario where the stocks are getting cleared but a surplus demand is not seen. There are no big orders or big demands and so entire manufacturing sector especially in India is under a big question mark for the future of huge profitability in this sector.
As far as domestic consumption is concerned, there are issues related to profitability. From one end, the retailers are demanding higher technical specifications and infrastructure requirements at the same price of finished good. At the same time, raw material prices are also not in favour of manufacturers. So how will the textile manufacturer survive in this race? The answer is to reduce the operating costs and manage profits.
So each and every company?having textile plants and machinery of more than five years?needs to adopt modernisation scheme. This can be achieved by opting for better technology; going for higher production output, products that consumes less power, less labour cost and have complete control on the operating process. In order to bring these changes, the manufacturer should not follow the techniques and strategies adopted by the fellow players or competitors. They need to assess their existing situation and understand the technology levels, productivity levels, maintenance program, waste management, target markets, workforce allocation and also the logistic cost.
It must be ensured that the better technology levels that are adapted must give higher production levels at the same operating cost achieved earlier. This strategy should be the key aspect to consider when we are thinking about modernisation. So concisely before heading to modernisation, we need to understand the current production programme and carryout the evaluation and bifurcation of machinery. We need to question ourselves and find answers for the following aspects:
So a manufacturer from his entire product basket must firstly finalise the profitable products and select only the one?s having good, reliable and consistent markets. Once the above exercise of finalising the product mix is done, we need to move to the next step that is analysing the technology of machines installed. We need to select the right machinery for finalised products; a compromise on technology front will reduce our profit margins as it affects the quality parameter of products. The wastage generated is also an essential parameter while selecting the technology. The wastage level must be as low as possible. So, after allocation and setting up of machinery as per the desired products and required quality parameters and maintenance cycle, we must run the production process as per pre planned programme to ensure that each and every machine will go into the maintenance cycle periodically. If the planned schedule is followed on a regular basis, it ensures that the wastage level remains low and higher production is achieved.
While selecting the quality aspects for our products, we must take into consideration the actual quality demands of the end users so that the entire production line is optimised as per the desired parameters, thereby giving appropriate quality at appropriate cost. This exercise will inform us whether we need to replace or change certain machinery accessories like rings, travellers, spindles or drafting systems on ring frames or similarly change various types of wires or do we need to carry out proper settings. It is necessary to check as setting changes as per the nature of fibers selected even in case of natural fibers. All these parameters setting needs to be done when there is change in the raw material. Similarly we need to have check on quality parameters of fabric and garments. While doing actual allotment of machines to workers we must understand that the worker will be working for eight hours in a shift. His job role should specify the type of work to be done per day and not the number of machines to be handled. This work concept was introduced by Frederick W Taylor on time and motion study which must be implemented in textile industry. This will make sure that the workers are not simply allotted number of machines to be operated on but are given tasks to be performed that specifies the quality checks to be carried out on the process parameters, machines to be attended, cleanliness to be maintained, etc.
This way the worker will act as an ambassador for set of machines he is working and will give much better quality results and hence will minimise the number of workers needed. For example, in case of ring frames with latest technology, the number of brakes are very less hence more set of machines can be given to single worker however due to stringent labour compliance laws we cannot give more than a predefined set of machines to a single worker against the agreements done earlier. So if we start by giving list of task to workers to be done on his shift everyday it will lead to better work allotment and optimise the work. It?s challenging, but very much need of the hour. It is the call of time to understand this concept and inculcate this method.
The other major cost factor after raw material is the power cost, which every organisation has to address today. The recent developments in renewable energy have made power generation through solar, wind and hydal much economical. To boost the installation of renewable power source the state and central government has given various subsidies. They have also launched schemes through which a manufacturer can park or give away excess power to state electricity grid and can use it as and when in need. A textiles plant be it spinning, weaving or finishing is having huge roof structures which are open spaces used only for covering purpose. This unused space on roof can be studied for putting up of solar panels thereby making maximum space utilisation with energy generation.
This is one way of reducing power cost by shifting to alternate power sources apart from this power consumption can be reduced by simply doing an energy audit or power audit which will identify age old machines that are consuming excess power a simple change in motors of these machines will also reduce their power consumption and they will start running at speeds desired for the operation thus increasing productivity. This reduction in power cost will bring down the operating cost considerably.
Another arguable topic under modernisation is waste management. As to my knowledge most of the mill owners will not agree that there is a scope for reducing waste in their mills. But a third party observations will be a neutral aspect to the problem as there will not be any barriers or blind spots to him in his study helping him in identifying the sources of waste generations and will help him give innovative ideas for wastage reductions.
Conclusion
Modernisation is a very tricky process. It aims at polishing the old to look as new but not completely shift to the latest. It basically is a process wherein it is tried to reduce the overheads. So when a modernisation is thought of [mostly], we tend to follow the records or concepts that are known or available in the mills. We must, however, come out with an assessment on case-to-case basis, re-assess our assumptions and then implement the solutions. There can be no standard process because every unit runs differently, on different practices, technology fronts, different work culture and many other aspects. Hence the modernisation simply doesn?t mean replacing the technology or bringing new machines but involves assessment of production, maintenance, quality, resource management, marketing channels, product basket, power, green energy and sustainable culture. Hence, a lot of aspects to consider and a third party analysis will always help the mills to look beyond the usual?s and come out with ice breaking changes that will ultimately result in high productivity at lower operating cost to maximise profits. We, at Suvin Advisors, have experts working in the textile industry for more than 30 years and are capable of carrying out modernisation assignments for mills. We believe in preparing business models with refreshing ideas and techniques that will help in identifying weak areas that remain unnoticeable but play a very important role in global competitiveness and increasing profitability. We take care of devising modernisation strategy, complete roadmap for implementation, re-designing utility systems, re-validation of marketing plan, HR framework, financial arrangements, training needs and quality related issues. We would use all our expertise to make existing textile plant more profitable and successful to reap higher profits.
This article is authored by Avinash Mayekar,
MD and CEO, Suvin Advisors.