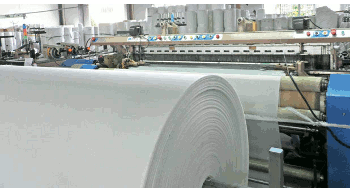
Development of filter fabrics for bag filters
The efficiency of the filter media used in a dust collector does not equate to dust collector efficiency; the filter media is just one component of the bag filter, and the filter bag is just one component of the dust collector system, reveal Dr HD Joshi and Pooja Shah. Bag house is a generic term for air pollution control equipment (APCE) that is designed around the use of engineered fabric filter tubes, envelopes or cartridges in the dust capturing, separation or filtration process. Bag houses can be found in virtually every industry ? foundry and steel production, pharmaceuticals, chemical producers, food manufacturers, etc.
The efficiency of the filter media used in a dust collector does not equate to dust collector efficiency; the filter media is just one component of the bag filter, and the filter bag is just one component of the dust collector system, reveal Dr HD Joshi and Pooja Shah.
Bag house is a generic term for air pollution control equipment (APCE) that is designed around the use of engineered fabric filter tubes, envelopes or cartridges in the dust capturing, separation or filtration process. Bag houses can be found in virtually every industry ? foundry and steel production, pharmaceuticals, chemical producers, food manufacturers, etc.
The selection of a specific material as filter media often depends upon the type of industry where the filter media is to be used. The type of material decides the maximum operating temperature of baghouse. Each application area has its requirements for dust filtration and no one fibre or fabric type can meet all these requirements. The characteristics of existing filter fabric which needs to be optimised are:
- Higher filtration efficiency
- Lower pressure drop
- Higher durability (longer life of filter media)
- Lower cost v/s performance benefit
- Better abrasion resistance
- Resistance to blinding/plugging
The ?one size fits all? concept has never been applicable to filtration and hence there is much scope for optimisation and development of filter fabrics.
If a filter fabric having greater filtration efficiency/lower dust emission, longer life, lower maintenance and cost can be developed, it would provide tangible benefits to the user.
Materials & methods
Bag filter fabrics were prepared by the weaving process from fibre glass yarn and from 100 per cent polyester filament yarn on 42-inch loom width. Woven filters have open spaces around the fibres. The weave design was varied with the application of the bag filter. Bag filter fabrics were woven in plain weave, satin and twill weaves. In all, four bags filter fabrics were developed with three weaves. Six samples of bag filters have been studied and comparative evaluations have been stated.
Nonwoven bag filter fabrics were procured and studied for comparison purpose only. The bag filter fabric samples studied in this project and their fabric constructions are as tabulated below:
Finishing of woven fabrics
Filter fabrics were treated (finished) so that they can withstand conditions encountered in a baghouse such as acidic and alkaline fumes, moisture or abrasion. Many of the treatments are mechanical surface treatments and others are chemical treatments of either the entire fabric or just the fabric surface. Mechanical surface treatments generally improve the dust cake formation on the filter and filter cleaning. Samples A, B and are given PTFE finish in order to improve efficiency.
DuPont? Teflon® PTFE TE-3864 was used for finishing filter bags.
Result & discussion
The bag filter fabrics developed by MANTRA (Sr. No. 1,2,3 and 6) and those procured (Sr. No. 4 and 5) were tested for mechanical properties, mass per unit area, air permeability, bursting strength, abrasion resistance and dust permeability.
I.Mechanical properties
Mechanical Properties of fabrics are given in Table 2 and it is observed that:
- The breaking strength (BS) and elongation of weft yarn is in most cases higher than that of warp yarn.
- The breaking strength of woven fabrics A, B and F is comparable with that of the commercial baghouse filter fabric (Sample I).
- The breaking strength values of samples A, B and F are higher than that of the commercial sample I and hence these fabrics can be expected to last longer.
- The mass per unit area (gsm) of Sample A is highest and comparable to that of the commercial baghouse filter fabric.
- A higher value of mass per unit area is indicative of a denser weave which may result in better dust filtration efficiency.
- The commercial baghouse filter fabric has a mass per unit area gsm of 754 g/m2 which is being used as a filter fabric in industrial chimneys. Samples A and F have similar gsm and hence can be expected to have similar dust filtration properties.
II.Air permeability
The air permeability of the bag filter fabrics was measured on the TEXTEST Air Permeability Tester FX 3300 by the Test Method ASTM D-737. Results of evaluation are given in Table 3.
In terms of dust filtration by bag filter media, higher air permeability means that the sample would allow more air to pass through so that the differential pressure drop decreases. Cake formation on the filter media is impeded which may also reduce filtration efficiency. Thus higher values of air permeability are likely to reduce filtration efficiency of the filter media.
To evaluate such performance, a comparison of the mass per unit area and air permeability values of the six samples have been made.
- Sample A has the highest mass per unit area (773 g/m2) and the lowest value of air permeability.
- Sample I (commercial sample) has a compact structure (754 g/m2) and a slightly higher value of air permeability. This trend is followed by all the samples ? as the mass per unit area of the sample decreases, the air permeability increases.
- Samples A and B are comparable to the commercial bag filter sample, both in terms of air permeability and mass per unit area.
- Of the two Nonwoven samples, sample J (PPS) and sample K (P84) & sample J has a lower mass per unit area with higher air permeability, while Sample K has a lower air per permeability with a more compact structure. The air permeability of sample K is comparable to that of the woven commercial sample I.
III.Bursting Strength
The bursting strength of the bag filter fabrics was measured on the Bursting Strength Tester from Globe Instruments, Ghaziabad, according to the test method IS: 1966-1975.
- The Bursting Strength of Sample A is the highest, followed by the commercial bag filter sample I and sample B. This implies that these samples may prove to be more durable in terms of sample strength.
- Of the two nonwoven samples J and K, sample K has a higher bursting strength than sample J.
- The results of bursting strength evaluation are in agreement with the fabric construction/weave of the samples. Samples with a compact structure and denser weave/structure have higher bursting strength values.
IV. Pore Size
The pore size of the bag filter fabrics was measured on a Porometer by ASTM D6767. The Pore size distribution has been measured and from the maximum and mean pore size, the average pore size of the 10 samples has been reported.
In terms of dust permeability, a compact structure and lower pore size can result in lower differential pressure drop and better filtration efficiency of the filter media. The reported pore size is the average pore size for the sample.
- Of the six samples, samples A, B, F, and I have the lowest values of mean pore size. The mass per unit area and construction of these seven samples are comparable and the mean pore size is also in agreement.
- The two Nonwoven samples have a mean pore size less than that of all the woven samples, indicating a highly compact structure.
V. Abrasion resistance
The abrasion fastness/resistance of bag filter fabrics was measured by rotary platform method on the taber abrasion fastness tester in terms of Taber Wear Index by ASTM D 3884-01. Results of abrasion are given in Table 7.
- Sample A have the highest Taber Wear Index, indicating lower abrasion resistance.
- Samples I, J and K have the lowest TWI, which implies good abrasion resistance. The number of cycles after which abrasion is observed is also comparable.
- Sample F also has a low value of TWI (as compared to samples I, J and K) but abrasion is observed after about 711 cycles while in Samples I, J and K, abrasion is observed after 1,200-1,500 cycles. This also indicates that samples I, J and K have better durability than Sample F.
Abrasion testing results indicate that samples I, J and K have the best abrasion resistance and durability.
VI. Dust permeability
The working trial of the bag filter fabrics for dust filtration was carried out on the PALAS Filter Test Rig MMTC 2000H. This instrument simulates the conditions encountered in an industrial chimney and measures dust filtration by the VDI 3926 guidelines.
The surface filtration of a powder (dust) takes place by the following steps:
- Penetration of dust.
- Loaded air through the filter.
- Separation of dust.
- Dust cake.
- Rise of pressure drop.
- Pulse jet cleaning.
The sample is evaluated under practical conditions of temperature, relative humidity and different dust types. The surface filtration of dust is measured in terms of the differential pressure or the pressure drop on the two sides of the filter. The lower the residual pressure drops (on two sides of the filter media), the longer is the expected life of the fabric. The lower the dust emission better is the filtration efficiency. The longer the mean cycle time is, the longer is the expected life time. Besides the tested samples, the results depend on:
- The test powder e.g. particle size distribution, particle material and dust mass concentration.
- The test conditions e.g. temperature, humidity, filter face velocity, components of the carrier gas
- The cleaning conditions e.g. pulse jet pressure.
The evaluation of the fabric is done on the basis of the residual pressure drop on the two sides of the media and the amount of dust which passes through the sample and collects on the (filter paper) at the end of the dust stream. The test sample is subjected to four test sequences:
- Initial 30 cycles with gravimetry, dedusting 5 mbar.
- Ageing dedusting 5 sec
- Conditioning dedusting 5 mbar
- Final Test dedusting 5 mbar, with gravimetry
Samples were tested at an air temperature of 250ºC (300ºC equipment temperature) on the Test Rig, initially for a pass/fail test, i.e. the bag filter were subjected to the four test cycles of 30 initial cycles, ageing, conditioning and the final test cycle using fly ash at 250ºC . The samples in which the 4 test cycles were completed were suitable for use as bag filters. The next step in evaluation was the gravimetry step i.e. the amount of dust collected on the total filter (filter paper) was measured. A comparison of these values is an estimate of the filtration capacity of the filter media. The results of dust permeability test are as tabulated.
- All samples have passed the test.
- Considering results of residual dust, sample F has the lowest values, followed by samples A and B, in order of increasing residual dust values.
- In terms of clean gas concentration, sample F has the lowest value followed by samples, samples A and B, in order of increasing clean gas concentration.
- Analysis of the residual dust values of samples A, B and F show that Sample B has the maximum value of residual dust. This implies that the dust passes through the filter. The clean gas concentration is also higher than that of other samples.
- Sample A also has high values of residual dust and clean gas concentration. Both these fabrics allow fly ash to pass through and collect on the total filter.
- Fabric F has lower values of residual dust and clean gas concentration, indicating better filtration property.
Conclusion
The efficiency of the filter media used in a dust collector does not equate to dust collector efficiency, the filter media is just one component of the bag filter, and the filter bag is just one component of the dust collector system. For bag filters, maximum flow rates, dirt holding capacity and materials of construction and style (microfibre, mesh, felt, binder, resin finished, seams or seamless, etc. vary by manufacturer. The design of the bag and materials of construction control the surface area, dirt holding capacity and maximum flow rates the filter can withstand. The dirt holding capacity of a bag filter varies gradually as the construction moves from a mesh or felt, single or multilayer construction to a pleated bag.
There are two types of dry filtration media in use today ? depth filtration media and surface filtration media. Depth filtration media requires maintaining a dust cake on the filter bag to achieve effective efficiency. Surface filtration media utilizes an additional barrier on the filtration fabric as the filtering layer. These fabrics (e.g. PTFE laminated) can achieve perfect efficiency, but the filtration fabric is just one of many components contributing to dust collection efficiency. Filter fabrics are tested for mechanical properties before use and application in a particular industry.
From a practical viewpoint, air permeability, abrasion resistance and filtration efficiency may be used to evaluate the performance of filter fabrics. Even though the results of dust permeability are a direct indicator of the performance of the filter fabrics in use, it must be remembered that the sample tested is a 6 inch (150 mm) diameter sample. Laboratory tests are indicators of the performance of the fabrics, but it is only when the fabric is placed in a dust collector under actual conditions, can its performance in use be gauged. Based on the properties tested samples, samples A and B are suitable as filter fabrics.
Dr HD Joshi and Pooja Shah are with the Man Made Textiles Research Association (MANTRA).