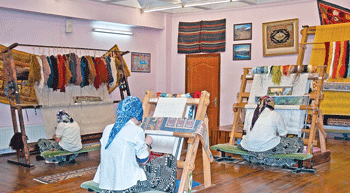
Uniqueness of Kanchis silk sarees
Kanchipuram is famous for two things - temple and silk. The traditional silk saree weaving industry of Kanchipuram is believed to be of time immemorial origin, writes R Haripriya and VR Giri Dev. Spirituality, secularism, culture, tradition, temples, worship have been divinely connected with the holy silk sarees of Kanchi.
Kanchipuram is famous for two things – temple and silk. The traditional silk saree weaving industry of Kanchipuram is believed to be of time immemorial origin, writes R Haripriya and VR Giri Dev.
Spirituality, secularism, culture, tradition, temples, worship have been divinely connected with the holy silk sarees of Kanchi. The production of Kanchi´s silk saree is as fascinating as it takes the final shape. What would explain a temple city of Kanchi as loads of people throng in for the daily search of purity, piousness and moksha? Kanchipuram is famous for two things – temple and silk. Daily thousands flock to Kanchi for the major silk saree purchases. While there are other silk saree centres in Arni, Dharmapuri, Salem, Rasipuram, Kanchi has always been considered as the silk capital. The Kanchi silk sarees have always been passed from mother to daughter as the throne of the king to his son in ancient India. The traditional silk saree weaving industry of Kanchipuram is believed to be of time immemorial origin.
Historians believe that it got the royal patronage during the period of the Vijayanagar kings. This to a certain extent is evidenced by the presence of a large member of weavers of Telugu origin. One remarkable feature about the process of making a silk saree is that the production method has not been changed much over the years. With the government keen on prohibiting the introduction of power or automatic process in the making of the saree, the industry continues in the old tradition of centuries. The innovativeness and craftsmanship of the Indian weaver could be clearly observed when one makes a closer study of the making of a saree.
Let us go into the actual processes involved in the making of the Kanchi sarees. Silk yarns from silkworms The tender mulberry leaves play an important role in the production of silk yarns. Mulberry leaves are fed by the silkworms. As a result, saliva is secreted from its mouth. Since it keeps secreting saliva, the saliva surrounds the silkworms. Hence it forms a nest called cocoons in which the silkworm lives. After a while, the cocoon is removed from the mulberry bush. The cocoons can be sold as a whole or they can be made into yarns and are sold. The cocoons are put into the boiling water. A strand of the yarns is taken and is reeled. If the yarn gets broken, it is taken again and connected. An average of 10-20 cocoons put up a yarn.
Raw material
The silk yarn is obtained from Chitlagutta from the state of Karnataka, which owns a better quality and is more expensive. Karnataka is the major supplier of silk through the Karnataka Silk Marketing Board outlet. This board sells three tonnes a month. Lately, Andhra Pradesh has become a renowned supplier of silk yarns. Assam and Kashmir contribute only a small amount. Thus 75 per cent of silk is brought from outside. Pure raw silk is used as the raw material for the production of Kanchipuram silk sarees. The raw silk is locally called Kora silk. The yarn is of rough nature and it has to be degummed to form soft silk. The warp employs a filature/the multi-end fine quality raw silk of denier 16/18 whereas the weft draws on the filature/chakra coarse quality silk of 22/24 denier. The raw silk is twisted as organzine or tram yarns for the preparation of warp and weft respectively.
Winding, doubling and twisting
The Kanchi sarees differ from the sarees made in other centres by sheen and weight. The difference arises right from the twisting of yarns. Silk reeling and twisting were separate processes when they were manually done. They become a single process after it has been mechanized. Traditional Kanchi sarees use twisted silk both in the wefts and the warps. They are twisted in the ratio of 7:10 respectively. This twist enables the saree t