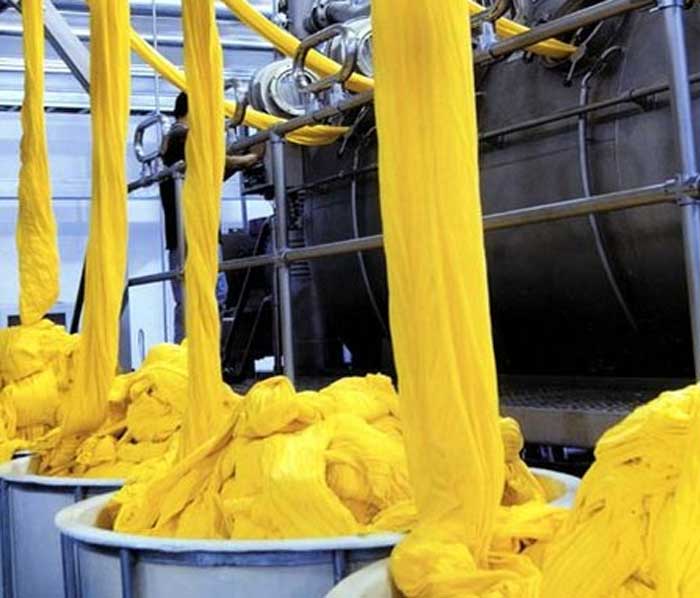
Emerging technologies in the field of textile processing
The environmental impact of solid waste formation, liquid effluent generation and the release of gaseous emissions during the textile wet processing is a major concern, says Dr Ashok Athalye.
Textile is a basic need of civilised human beings and is considered to be the mother of industrialisation as the start of the Industry 1.0 era is associated with the first mechanised weaving of textile fabric. The past two centuries witnessed various technological innovations in man-made fibre developments, hi-speed machines, specialised colourants, functional effect chemicals, etc, which ushered in the era of automation and digitisation referred to as Industry 4.0.
However, during the entire value chain of the textile manufacturing domain from the Farm to Fashion segments, wet processing is considered to be the weakest link owing to the numerous complexities involved in terms of varying fibres, forms in which they are processed, types of machinery used, complicated methods adopted to meet the end use expectation and the most importantly the emerging demand for sustainability.
The environmental impact of solid waste formation, liquid effluent generation and the release of gaseous emissions during the textile wet processing is a major concern. The academic as well as industrial research in technological developments is focussing on ways to minimise or harness the environmental impact of textile manufacturing. Optimising utility (conserving water, energy and time of textile processing), ensuring sustainability (in terms of ecology, economy and social aspects) and circularity (reduce, reuse and recycle) are the commonly used terms.
The use of textiles is not only restricted to apparel wear but is also rapidly increasing in the field of home décor and technical applications. The rising consumer expectations in terms of product utility and the stringent eco-conformance norms decided by international organisations/brands are pushing textile manufacturers to adopt innovative and novel technologies to cope with:
- Maintain pace with changing consumer requirements due to fast fashion
- Meet the basic expectation in terms of quality consistency
- Ensure business commitments for timely delivery
- Provide effective and comprehensive solutions as a smart service supplier
- Conserve water, energy, time and human resource for saving utility
- Attain sustainable growth through eco-conformance
Thus, to meet such expectations and demands of various stakeholders in the textile value chain, it is imperative to continuously innovate and develop technologies which can fulfil the growing needs.
Given below are some such recent developments in various segments of textile processing;
Fibres
The conventional substrates are getting replaced by novel fibrous material extracted from various renewable sources.
- Natural: Widening gamut of natural vegetable cellulosic fibres for apparel and home furnishing applications for self-use and in combination as a blend component of varying extent. This includes fibres extracted from Banana, Hemp, Elephant grass, Napier Grass, Corn husk, etc. The innovative and cost-effective fibre extraction processes include using biotechnology to reduce time and water consumption and achieve optimum yield. These fibres are used in varying blend ratios and other conventional materials for making decorative components. Modified protein-based fibres from collagen, soya milk etc.
- Regenerated: Semi-synthetic fibres made out of renewable natural resources like lactic acid from sugar cane and corn to produce Poly Lactic Acid (PLA) fibre, also called natural Polyester.
- Functional: The emerging demand for technical textiles has prompted development in speciality hi-tech fibres, which are synthetically produced to achieve the specific end use applications. Some of these material include
- Aramid – aromatic polyamide
- Asbestos – silicate mineral
- Carbon -Lightweight, high strength
- Ceramic –Alumino-silicate
- Glass – Alumino-boro-silicate
- Metal – Pure and alloys
- Modacrylic – Acrylic, vinyl chloride, vinyl bromide
- UHMWPE – high modulus, ultra-high molecular weight polyethylene
Machines
The conventional high liquor ratio batch-wise processing machines are paving the way to low and ultra-low liquor ratio technologies.
- Yarn: The modified package dyeing machines based on Pulser or Wave technology work on a very low liquor ratio of about 1:3.5. This drastically reduces water consumption along with the energy needed for the heating-cooling steps and the time required for filling and draining at each step.
- Knit: The soft flow machines having compartmentalised systems and working at MLR of about 1:4 substantially reduced water, energy and processing time.
- Woven: The pad-humidifix processing technology is getting wide recognition as one of the fastest-adopted technologies for continuous dyeing of cellulosic fabric by reactive dyes.
- Denim: Foam dyeing of indigo by bubbling nitrogen as an inert gas is considered to provide the desired ring dyeing of yarn by a one-step process for optimum colour depth and avoid undesired premature oxidation.
- Garment: The dyeing and washing-off of made-ups and garments using Nano-Bubble Technology (NBT) by blowing air in water substantially reduces the volume of liquor and thus saves water and energy.
Water
Being a universal solvent, abundantly available and a negligible cost component, textile processing uses water as the medium of application, this is why it is traditionally called wet-processing. However, with growing concerns over effluent generation and pollution of water bodies, the non-aqueous method of dyeing is gaining importance.
- Air dye technique: Polyester dyeing using low molecular weight Disperse dyes using hot air is considered a novel technique which makes use of the typical low temperature sublimation property of these dyes.
- Super critical fluid: Utilising carbon dioxide gas as a freely available atmospheric component by converting it into its liquid form under certain temperature and pressure conditions is another unique technology for water-less dyeing.
Colourants
Though no new dye range was developed after the introduction of reactive dyes in 1956, many new products within the existing class of dyes were introduced, which filled the gaps in the shade gamut and enhanced the extent of colour fixation.
- Vat dyes: Micro and nano disperse variety for dyeing by pigmentation process
- Cationic Reactive dyes: For salt-less exhaust applications
- Fluorescent pigments: For achieving Neon shades
- Disperse dyes: For high wash and light fastness
- Chromic Materials: Colourants that behave differently under varying conditions of temperature, pH, moisture, pressure, etc
Chemicals
Textile processing is a chemical-intensive segment, where a large quantity of non-aqueous support components is used for intensifying the application.
- Basic: Different acids, alkalis, salt, oxido-reductive material, thickeners, etc, are needed at various stages of processing, which eventually get discharged into the effluent stream, causing pollution issues. Such chemicals are being replaced by eco-friendly alternatives using green chemistry where the extent of chemical concentration and the environmental impact are minimised.
- Auxiliary: The conventional chemistries of support components like surfactants, dispersants, sequestrants, etc., which impart or enhance the processing parameters, are being replaced by non-toxic, eco-friendly substitutes which make use of biotechnology and plant-based products.
- Effect: Typically, the finishing chemicals which impart desired perspective and protective effects fall in this category. The novel fluorine-free stain repellants, nan-phosphorous flame retardants, non-formaldehyde wrinkle-free finishes are being used.
Processing
Many innovative technologies have been developed and are being exploratively used to evaluate performance efficacy. Some of these are listed below
- Ultrasonic: Generates kinetic energy for dye diffusion
- Microwave: Vibrational energy for optimum coloration
- Electrochemical: Electricity for reduction of Vat and Sulphur
- Ozone: Bleaching of cellulosic material using ozone as oxidant
- Plasma: Surface modification for improvement in dyeing
- Laser: Surface modification to improve the dye uptake
- Morphology: Structural coloration due to interference of light
Acknowledgement
The author would like to thank the Institute of Chemical Technology (ICT) Mumbai for providing this opportunity to share relevant information.
About the author:
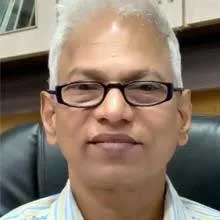
Dr Ashok Athalye is a Professor of Textile Chemistry and Vice-President at Technological Association (ICT- Mumbai). He is also the fellow of the Society of Dyers and Colourists (FSDC-UK) and Fellow of the Indian Chemical Society (FICS).